Large Panel System design by Curtins enables survey and repair of pre-cast towers and removes the potential risk of disproportionate collapse in the event of gas explosions.
Curtins was established in 1960 in Liverpool and has been at the forefront of innovation in assessing and repairing low-, medium- and high-rise housing for nearly 40 years, operating with a team of nationally recognised experts across 14 offices. Its latest innovation for high-rise buildings removes the potential risk of disproportionate collapse in the event of gas explosions.
Curtins has investigated, appraised and developed repair solutions for thousands of pre-cast concrete and non-traditional homes across the UK. It has been recognised as the leading expert for this work since the early 1980s, when the team instrumental in the development of the PRC Homes Ltd licensed repair schemes and produced the first licensed repair scheme for non-traditional housing – No. 001 for Cornish Mansard PRC houses.
The consulting engineer’s latest innovation is a solution for pre-cast concrete ‘Large Panel System’ (LPS) high-rise buildings. LPS buildings do not have a structural frame and are constructed using interconnected concrete panels supporting the concrete floors. As a consequence, LPS buildings are considered at risk of disproportionate collapse in the event of an explosion within part of the building, if they were not originally designed to withstand the forces from such an event.
Curtins was invited to design a retrospective solution to prevent disproportionate collapse to the LPS buildings owned by for Birmingham City Council. In simple terms, their innovative design involves the installation of a steel brace on the outside of the tower block that ties the external loadbearing concrete walls, and the upper internal loadbearing walls, to the floors. This brace enables those components of the building to act together to withstand the forces in the event of explosion, with the building remaining structurally stable. The steelwork is insulated with a non-combustible External Wall Insulation and clad with a more attractive render.
The benefit of this innovation is to minimise the disruption and intrusion to the building’s occupants whilst the installation work is being undertaken, as it only requires the decant of certain floors rather than the whole block. The end result is a significantly safer, warmer, visually more-attractive place to live, with improved thermal performance and an associated reduction in energy consumption.
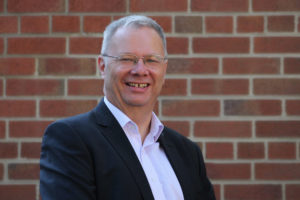
The new solution is to be trialled by Birmingham City Council this year on an LPS high-rise block in the three city areas.
John Healey, an Associate at Curtins with over 35 years’ experience in this type of work explained: “We’re pleased to be introducing this new solution for LPS buildings.
“The lack of a structural frame in LPS towers means that these buildings are potentially at risk of disproportionate collapse. Piped gas heating has therefore been banned to minimise the possibility of a gas explosion. However, the buildings are still susceptible to non-piped gas explosions and their concrete façade means they’re thermally inefficient.
“Primarily, our solution will ensure that in the event of an explosion, tenants will be able to vacate the building safely. The introduction of our innovative galvanised steel frame and cross-stitching on the upper levels will prevent deflection of the loadbearing walls, which can cause them to collapse. The second major benefit is that the non-combustible external wall insulation and cladding will make the buildings much warmer, which is great news for the tenants and the environment.
“Many local authorities in the UK have one or more LPS buildings, so our future strategy will be to introduce the solution across the UK to improve safety nationwide.”
Birmingham City Council is the largest social landlord in the UK and the Curtins solution is the first design innovation for LPS tower blocks that has been adopted.
Curtins operates in each key stage of the built environment lifecycle through their seven areas of specialism. These include civil and structural engineering, transport planning, environmental, infrastructure, geotechnical, conservation & heritage and principal designer services.
To find out more about Curtins’ specialisms and survey and repair services, visit www.curtins.com