Jonathan Ducker, Head of Regulatory Affairs at Kingspan Insulation, considers how social housing providers can insulate residents living in ‘hard to treat’ properties from fuel poverty, by ensuring existing homes retain heat effectively, and offers advice on installing internal wall insulation.
The latest annual fuel poverty statistics report show that the average fuel poverty gap increased by 66% in real terms between 2020 and 2023 due to rising energy costs [1]. For social housing providers, a key step to protecting occupants against this is by ensuring existing stock retains heat effectively. Whilst substantial progress has been made retrofitting loft and cavity wall insulation, recent data shows that just 26% of solid walled social housing properties feature wall insulation [2]. These untreated properties tend to be the oldest and least energy-efficient, leaving occupants at significant risk of fuel poverty.
The simplest approach to addressing these so called ‘hard to treat’ properties is by fitting external wall insulation (EWI) systems which wrap around the existing building. However, EWI solutions will not always be feasible, meaning the only option is to fit internal wall insulation (IWI). When designed and installed correctly, IWI solutions can significantly reduce heat losses and support lower heating bills. To avoid unintended consequences, however, it is essential that this work is carried out with careful planning and consideration for the building and its context.
Moisture open or closed
Before fitting any internal wall insulation, it is essential to fully understand the moisture properties of the existing building and walls. Many solid walled properties constructed prior to the 1920s feature permeable wall constructions that allow moisture to slowly pass through them; however not all walls are permeable, or have become much less so, since original construction. In an uninsulated property, heat from inside the property and from the sun helps to dry the wall.
Once insulation is fitted however, the heat loss from the inside will be greatly reduced, interrupting the drying process and potentially allowing vapour within the construction to condense interstitially (between layers). An appropriate condensation risk assessment can determine this risk and the walls capacity to handle any condensation that might form.
There are two ways to address vapour in a wall construction. The first of these is using a ‘vapour open’ system with permeable materials that can, to a point, buffer moisture. The drawback is that buffering capacity is limited beyond a certain point, which means that walls will typically need to be insulated to a lower level than might otherwise be preferred.
The alternative is a ‘vapour closed’ solution, using moisture closed materials, such as phenolic insulated plasterboard. This approach relies on the wall construction being (or becoming) suitably resistant to the level of driving rain present and requires a vapour control layer (VCL) to be installed to prevent or reduce, to a safe level, the interstitial condensation that might occur within the improved wall construction.
Phenolic boards are typically more thermally-efficient than moisture open alternatives, meaning it is possible to effectively insulate walls with a slimmer thickness — maintaining internal space. When fitting these boards, all junctions must be carefully designed and installed to ensure both VCL and insulation run continuously across walls and junctions.
Which approach is appropriate for a building depends on the project specifics, its use, location, construction, condition, significance, ventilation, moisture load and level of heating; which is why a proper assessment and development of a plan for improvement is so important.
Alongside the choice of insulation, there are a number of other factors that need to be carefully considered before carrying out IWI.
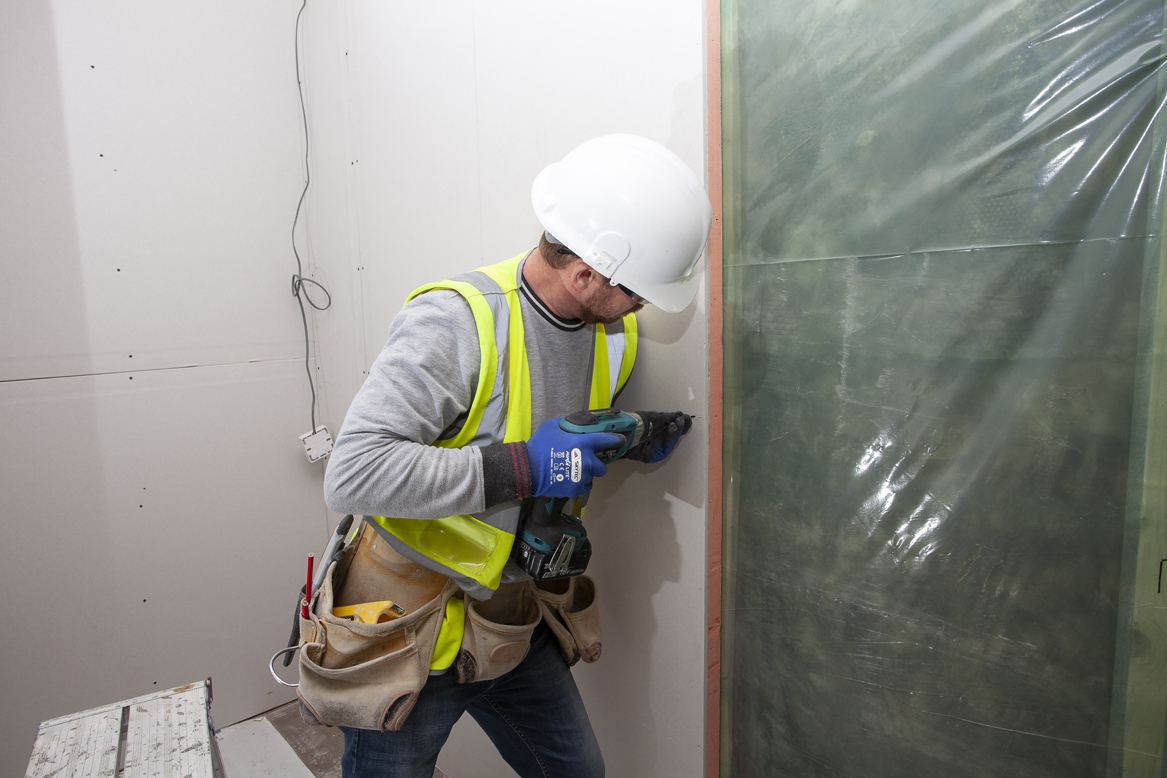
Whole House Approach
PAS 2035 sets out a clear process for assessing existing properties and developing an improvement plan, which is sensitive to their particular design and circumstances — this is known as a Whole House Approach. This improvement plan is clearly and logically phased and works must be carried out by contractors certified to PAS 2030:2023 — a supporting installer standard for energy retrofits. The works and supporting documentation are logged in a Property Hub, which social housing providers can access — providing a golden thread of information. There is also a clear post-handover evaluation process to ensure measures are performing effectively and, where necessary, to address any issues.
Where IWI solutions are considered as part of the plan, a number of assessments will be carried out including:
- A full survey of the building characteristics and condition (any issues must be addressed prior to improvement work commencing).
- A moisture risk assessment to BS 5250:2021 and driving rain risk assessment.
- An assessment of internal ventilation (IWI solutions can significantly reduce air-leakage from a property).
- Insulation details that consider interaction with other elements and adjoining properties (this may recommend the installation of additional insulation in the floor, roof or on party walls).
By adopting this Whole House Approach, it should be possible to identify the most suitable IWI solution for the property and deliver a retrofit that provides the energy savings expected without unintended consequences.
Long-term plan
Research has shown that retrofit work is expected to represent over 90% of the required building emissions reductions in the UK for us to meet our net zero emissions goal [3]. Addressing so called “hard to treat” solid walled properties is a key step in this process and is also essential to safeguard occupants from fuel poverty. By adopting the PAS 2035 framework, social housing providers can ensure that where IWI solutions are required, they are properly designed and installed with clear consideration for the existing building.
1. Annual fuel poverty statistics report 2024, Department for Energy Security & Net Zero
https://www.gov.uk/government/collections/fuelpoverty-statistics#2023-statistics
2. English Housing Survey 2022 to 2023, Department for Levelling Up, Housing & Communities (Chpter 5, Energy Efficiency)
https://www.gov.uk/government/collections/english-housing-survey-2022-to-2023-headline-report
3. Global retrofit Index, Kingspan: https://www.kingspangroup.com/en/sustainability
/product-sustainability/global-retrofit-index/
Header image: Kingspan Kooltherm K118 Insulated Plasterboard features an integral VCL and has a thermal conductivity of just 0.019W/mK