As offsite manufacturing and prefabrication methods grow in popularity, Paul Arnold, Product Manager at Remeha, looks at the benefits of applying these techniques to public sector heating refurbishment projects.
Offsite manufacturing is on the rise, driven in part by government policy to favour this construction method on all publicly funded projects. With reports of 30% cost and time savings, tighter quality control, improved safety and reduced waste, it offers a cost-effective approach to high-quality construction.
But offsite manufacturing delivers benefits beyond the construction industry. When it comes to HVAC, and to commercial heating plant in particular, using bespoke prefabricated equipment can achieve significant efficiency benefits for both the contractor and end-user throughout the lifecycle of the products.
Heating has been identified as a natural target for efficiency improvement, particularly in the UK’s older building stock. As commercial boilers are still the heartbeat of many non-domestic buildings, whether the sole provider of heat or operating in a hybrid system, ensuring that they operate efficiently should be a priority. But while boiler replacements can transform the energy performance of a building — reducing gas consumption by as much as half, in our experience — they are often carried out in challenging circumstances.
Space limitations within plant rooms, access constraints and tight project schedules are just some of the hurdles that may need to be overcome when carrying out a boiler upgrade. Hence the growing use of offsite fabricated, bespoke-designed rig and cascade systems to achieve time and space-saving solutions for multiple boiler installations.
Bespoke to requirement
Installing multiple advanced condensing boilers in a cascade configuration is a highly effective means of meeting a building’s heat demand — resulting in greater efficiency, improved reliability and more straightforward, non-disruptive maintenance. Typically, manufacturers will provide site-assembled cascade systems for up to 10 wall-hung boilers. But manufacturers like Remeha also offer bespoke offsite rigs for any number of wall-hung boilers. The layout can be specified by the designer — in-line, back-to-back, ‘L’ shaped or any other type — as can the header extensions and connections.
Where a high heat output is required, there is the option to use an offsite fabricated cascade arrangement. This is available for up to eight floor-standing boilers with an individual heat output of up to 300kW.
Project-specific controls can also be integrated into the design to optimise boiler and system efficiency. The boilers are delivered to site on a wheeled unit or can be designed to split into smaller modules for simple re-connection where access is particularly restricted. Quality assurance is also high as the units are produced under factory conditions with pre-release testing.
So how and where are these bespoke rig and cascade systems being used?
Space and time saving solution
A recent example is the boiler replacement project carried out by contractors TSS Facilities for Medway Council at Gun Wharf, its main council offices in Kent. TSS Facilities recommended installing five compact Gas 220 Ace floor-standing boilers on a bespoke-designed cascade arrangement as the most efficient means of meeting the heat load within the limited available space.
Minimising heating downtime was a major consideration as the offices needed to remain operational throughout the upgrade. So Remeha worked with TSS Facilities to design a bespoke pipework arrangement that would save on-site time and labour while achieving the most effective use of space.
A Plate Heat Exchanger (PHE) was integrated into the design to segregate the boiler circuit and heating circuit, and so optimise boiler performance and longevity. 3D drawings were produced to define the design and provide early visualisation of the layout. These then formed part of a comprehensive documentation pack for the Council to assist with future servicing and maintenance.
“Having the option to design the position of the PHE and pump ahead of installation meant that we could improve access,” says TSS Facilities’ Mark Basset. “And while the pipework was being configured offsite, we were able to work on the system pipework, which sped up the installation process.”
Once the equipment was delivered to site, TSS Facilities bolted together the boilers, pipework connection components and the PHE, on its wheeled frame, and connected them to the existing system.
“This installation technique enabled the Council to control the shutdown period required to complete the contract,” comments consultant John Richardson. “The fully modulating Remeha boiler plant, in conjunction with upgraded controls, has greatly enhanced the building’s efficiency and the Council’s carbon footprint.”
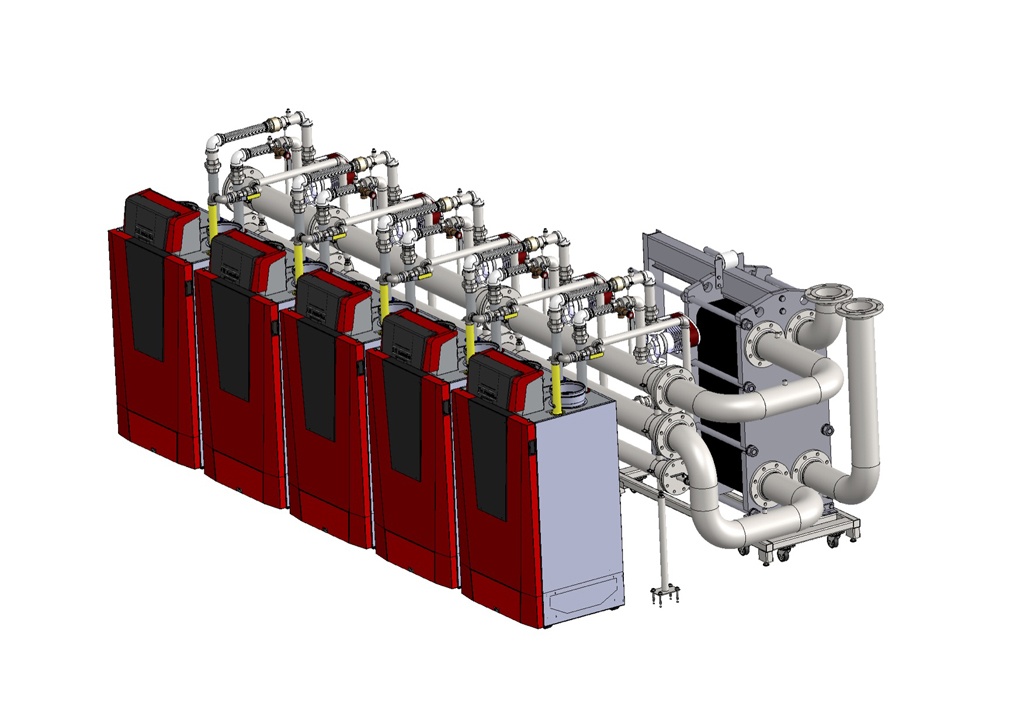
Greater planning flexibility
School buildings also benefit from applying offsite heating solutions as the rapid installation process enables more school heating systems to be refurbished within the same fixed time frame. The safer conditions and rapid changeover also enable greater planning flexibility as these projects no longer need to be restricted to the summer holiday period.
Bridgemary School in Gosport is a case in point. To overcome the combined challenges of restricted space and a tight installation schedule, Ridge and Partners LLP specified installing six Quinta 115 wall-hung condensing boilers and a PHE on a Remeha bespoke-designed rig. Integrated into the rig design are pumps specifically selected for the duty required for PHE operation, an expansion vessel, a pressurisation unit, and a dosing pot to ensure good condition water.
On this project, the controls were pre-wired to enable even faster connection to the new Building Management System control panel.
“The bespoke rig was great,” adds contractor IDWE’s Paul Neve. “It was wheeled straight off the tail lift and into place, saving us a lot of valuable time.”
Better performing buildings
In some of the nation’s older buildings, replacing old and inefficient boiler plant with higher efficiency condensing boilers may be both the most cost-effective and most practical solution to creating a better, more comfortable building.
Solutions like the offsite fabricated rig and cascade successfully remove the hassle factor from heating refurbishment. With greater design flexibility, it is easier to meet individual project and customer requirements and achieve a higher quality of installation. Whole-life boiler performance is addressed with full documentation and BIM files supporting asset management. And as costs, size and specification are all fixed and in place, the project is delivered on time and on budget.
Rapid, high-quality solutions like these will play an increasingly pivotal role in raising building efficiency. The future is bright for offsite.