The benefits of offsite construction are well documented. And yet, even though it’s becoming more commonly used across a wide range of different sectors, it’s still typically seen as a new process — a myth that its ‘Modern Methods of Construction’ label does little to dispel. And despite it offering a host of benefits, it’s all too often distilled down to a simple cost-time saving. Here Ryan Geldard, Operations Director at offsite manufacturer and contractor, M-AR Offsite demonstrates how it has been making the theory of offsite work in practice so that the benefits can be felt by all involved.
M-AR is currently working with Newham Council in London on a large school extension project at Little Ilford Secondary School. The extension has been designed to incorporate several new classrooms and corridors, a SEND block, an activity studio and a new underground car park area. A hybrid offsite construction method was specified and is currently being delivered by M-AR, but what was it about this project in particular that necessitated such an approach?
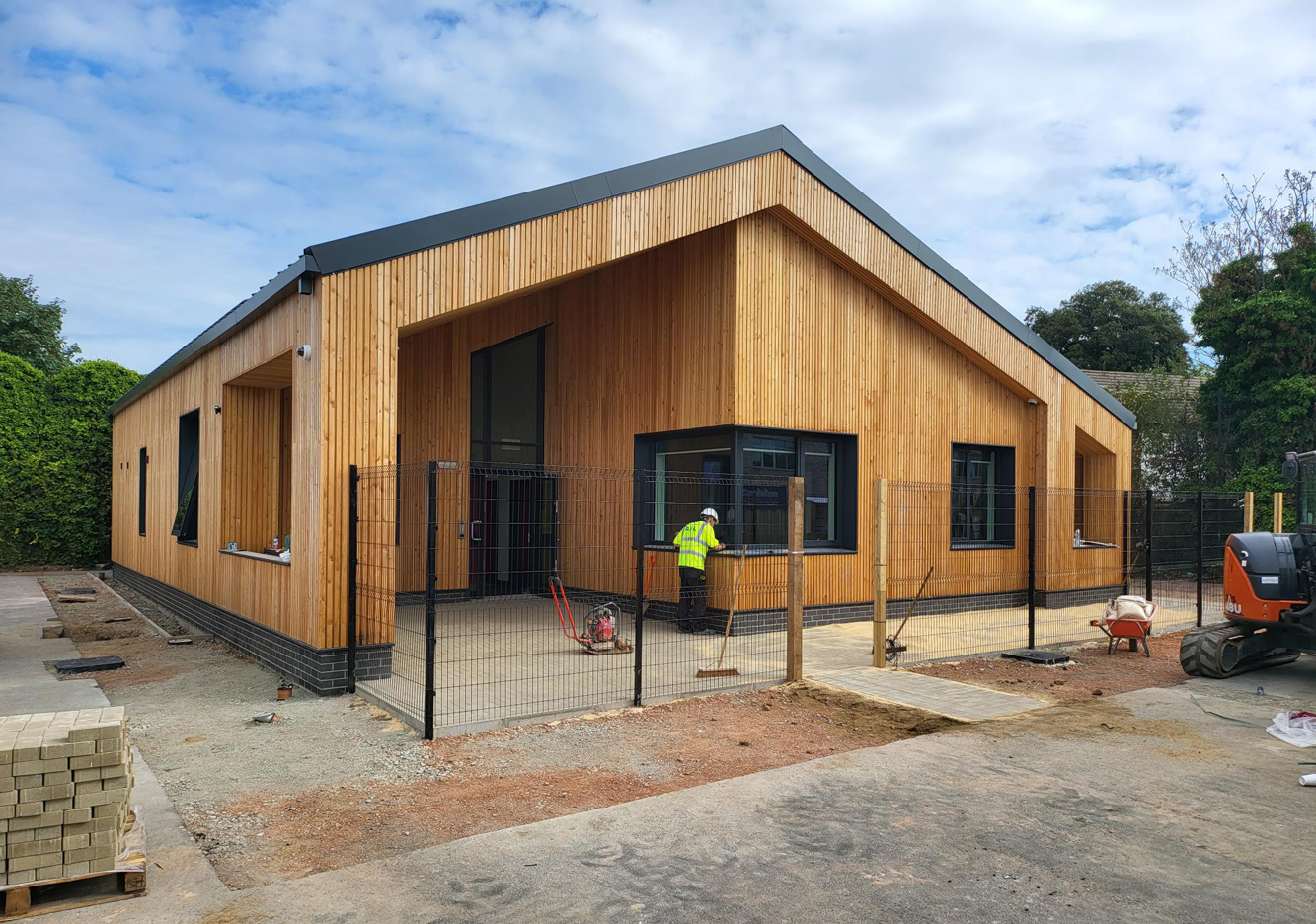
Space
The footprint of the proposed site for the school extension, being on the same ground as the existing school, was extremely tight and posed a major challenge. At certain points the new school building is only around 2m away from the existing building — which meant a traditional build would have been considerably more difficult, especially if more scaffolding had been required around the building for access.
By opting for offsite construction in the most part, this reduced the need for access scaffolding to just three sides, with modules manufactured in M-AR’s factory before being transported to site, positioned and carefully installed safely one by one. What’s more, the level of finish achieved in the factory vastly reduced the number of trades required onsite at any one time — again an important benefit given the size of the site.
Not only was the site itself tight and challenging — so too were the access routes as the school sits in the middle of densely populated residential area. With this in mind, the M-AR team designed the individual modules to fit comfortably on the size of transport permissible and practical for the area, without impacting on the completed project. The offsite element of the project was split into separate modules, each designed for ease of manufacture, delivery and installation, which fit together like a giant 3D jigsaw puzzle on site.
It was also the issue of space that dictated the need for adopting a hybrid approach on this project. the proposed new extension was to take up part of the school’s existing car park, and with parking at a premium in the area this had to be maintained, which meant sinking the car park underground and building the new school block directly above.
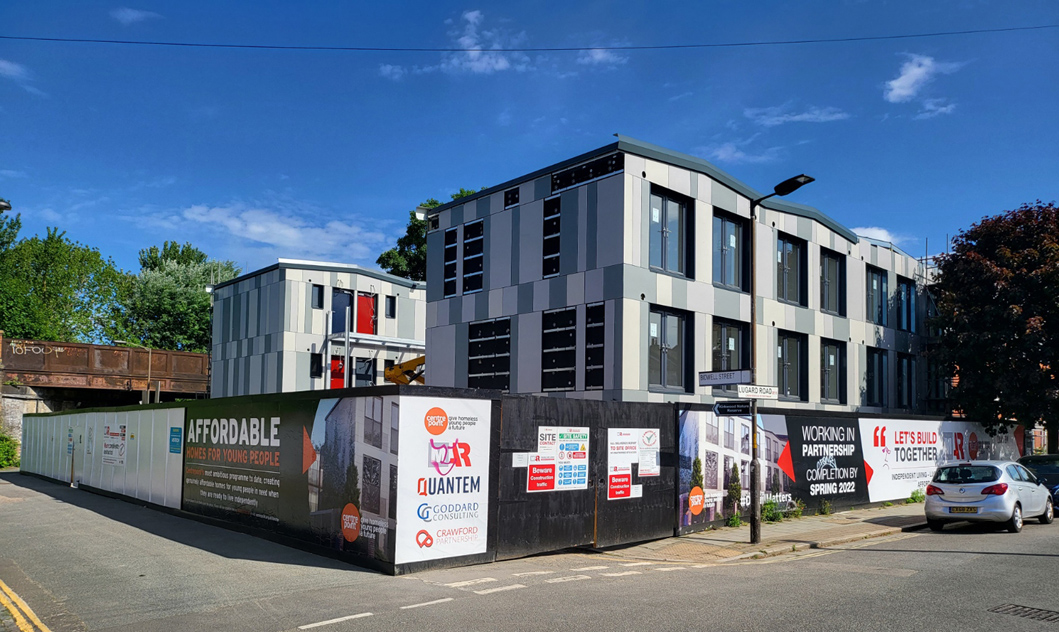
Safety
As is often the case with a refurbishment or extension project such as this at Little Ilford school, works had to be undertaken primarily on a live site. With the busy school in full use throughout the project, except the set holiday periods, safety had to be paramount to protect staff and students as well as site teams. In fact, so close was the site to the school itself that site teams had to contend with a football flying into the site from the school grounds on more than one occasion.
Moving much of the works off site and into M-AR’s factory meant the time required to complete the project on site was significantly reduced and so too was the number of trades needed and deliveries to and from the site. Making sure that all connections are designed to be bolted together rather than welded and that roofs are a welded system which removes the need for hot works with naked flames, is one way M-AR is able to reduce fire risks on site, without compromising on either the build schedule or the integrity of the building.
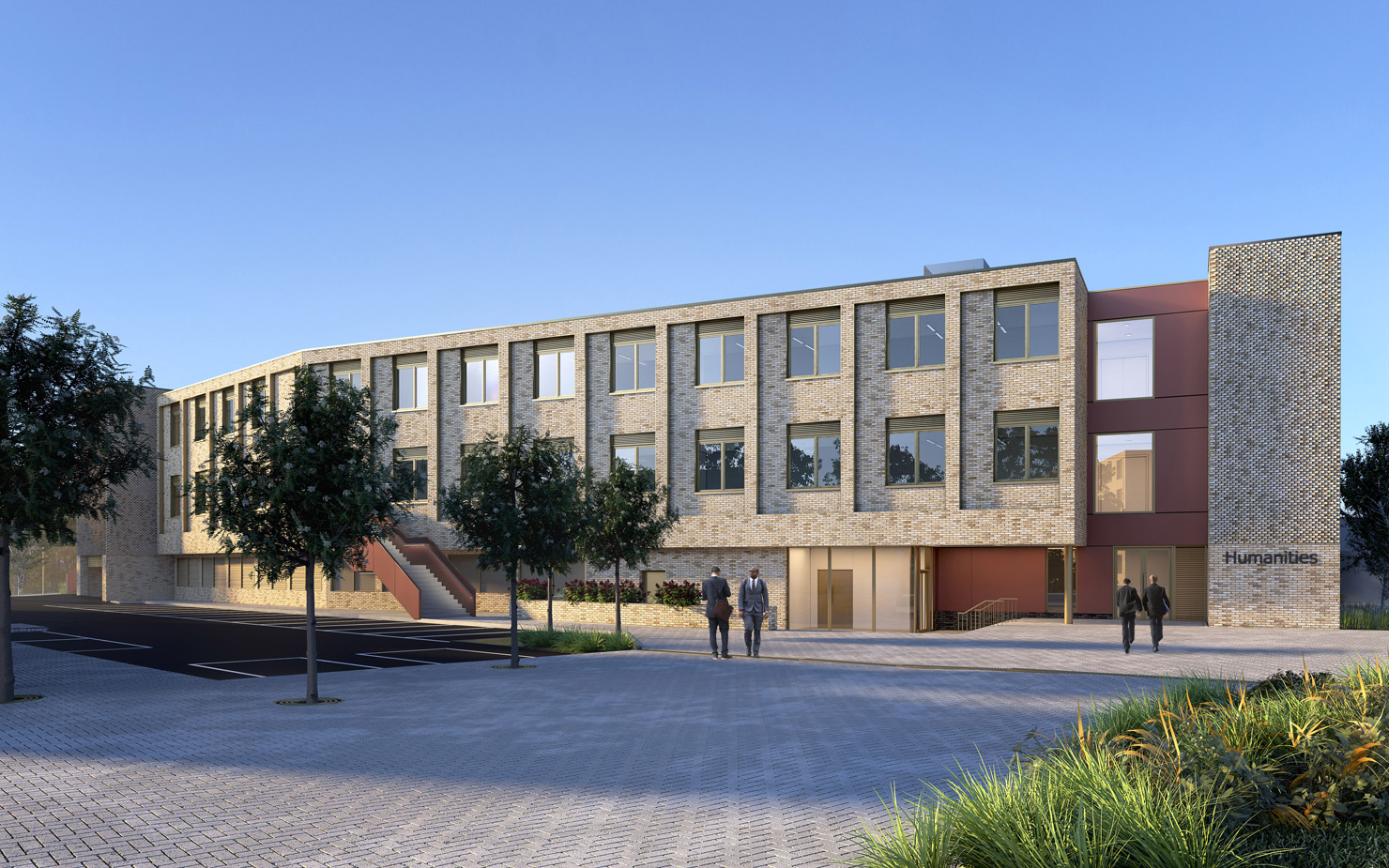
It’s too simplistic to think that offsite is always the more cost-effective option, when compared to traditional build, although if time is money, being more efficient will have a knock-on effect in terms of cost. Being able to carry out groundworks onsite and manufacturing the required modules offsite concurrently speeds up the process, typically resulting in a build programme around 50% quicker than a traditional build.
Additionally, manufacturing in a controlled environment removes the risk of delays due to poor weather conditions and the quality control process minimises the degree of snagging required on project completion. It also uses less waste, with materials bought in bulk and used as needed across multiple projects — infactory build processes mean that a use can often be found for offcuts that would, on a traditional building site, most likely be thrown in a skip.
That aside, a major benefit, particularly to local authorities working within set budgets, is the fact that offsite typically offers a greater level of cost-predictability — giving clients peace of mind from the outset.
By working collaboratively together, M-AR was able to ensure both aspects of this hybrid build dovetailed perfectly together — bringing the client the best of both worlds and delivering a stunning new school area safely and efficiently in a challenging environment.
Header image shows Little Ilford School on the production line at M-AR.