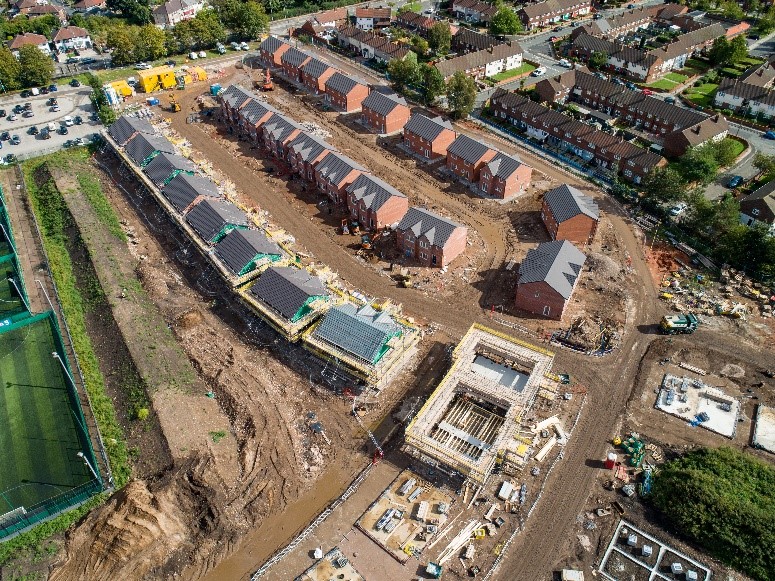
Construction, property and facilities company, The Sovini Group, is investing in offsite construction as part of their ongoing Net Zero Carbon Commitment.
The Group, which boasts an end-to-end supply chain, is supporting its wider environmental strategy with its latest initiative in the form of adapting raw materials for the new-build construction arm of the business, Sovini Construction. The highly advocated method of construction is set to facilitate the Group’s development framework to deliver 1,000 new high quality and affordable homes within the next four years.
The Group’s newest shift in sustainable construction management is the latest in a longline of ecological and biodiverse plans for delivering affordable social housing across the North West.
Time for timber
The structurally graded timber is sourced from Scandinavia and delivered to the Group’s independent builders’ merchant, Sovini Trade Supplies. The climate-smart raw material is then transferred to a local Merseyside-based organisations, timber frame specialist SticX. The award-winning team at SticX use the latest 3D CAD software to integrate the main architectural design of the structures. Once constructed using the PEFC certified timber, the frame is compartmentalised and transported to site where it is erected.
The Sovini Group’s timber framed homes provide a significantly lower carbon footprint through its manufacturing, reducing energy consumption throughout its lifetime and locking-away atmospheric CO2 for generations.
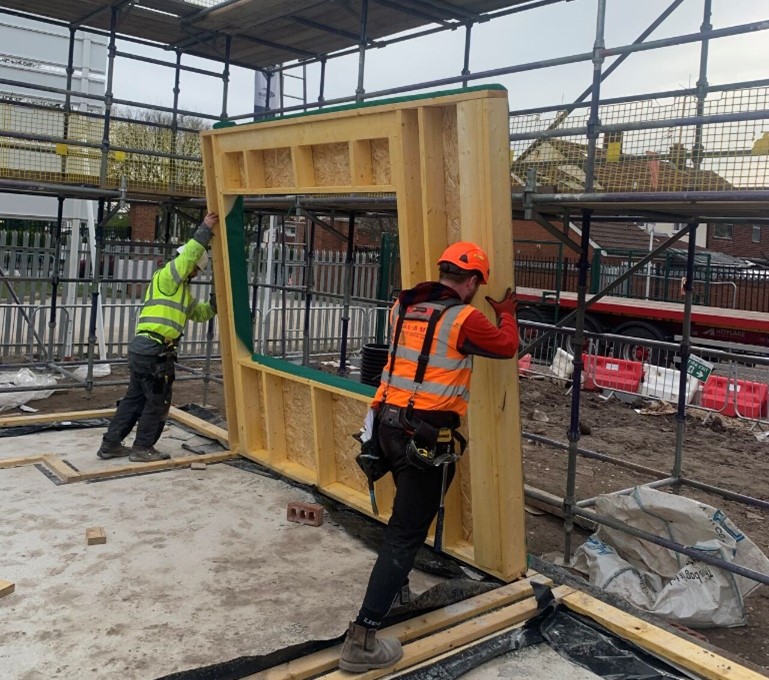
John Maddock, Director of SticX said: “Timber Framing is a great solution for The Sovini Group. For a client who’s genuinely concerned about sustainability it scores highly. By partnering with them, we can help develop improved solutions to save money and time. Ultimately, using timber frames means they can provide higher quality houses for their clients. We’re also a local company, so their spend stays local and benefits the Merseyside economy. We’re delighted to share our expertise with such an enlightened and progressive client.”
The Group uses recyclable materials which is designed to achieve superior levels of fabric performance, suitable for their projects which are seeking to achieve the very highest fabric efficiency, airtightness standards, and sustainable credentials.
The Sovini Group recently welcomed timber frame specialist SticX to its flagship Morris Meadows development in Merseyside to view the environmentally friendly materials come to life.
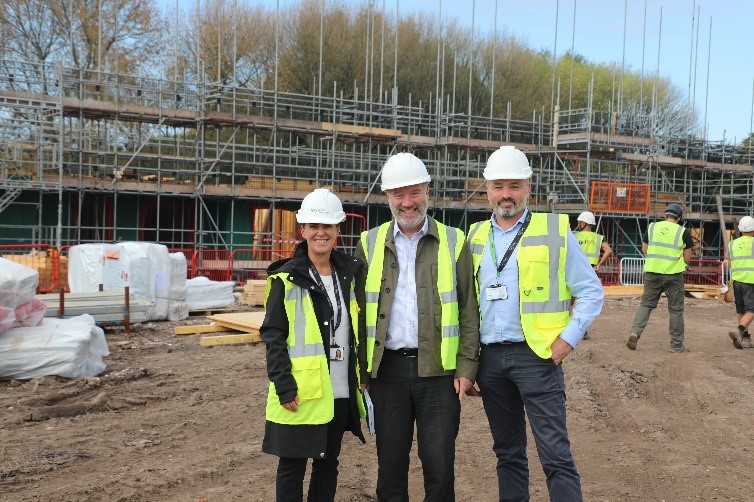
Sustainable social housing
The Sovini Group create thriving and inclusive communities which are well-integrated into wider urban systems. The offsite construction has proven performance, providing an advantageous construction method for affordable housing and with the Group’s timber frames being produced offsite and delivered in a prefabricated form, construction times to make a building ‘wind and watertight’ can save as much as 30% over that of traditional construction.
Employing over 800 colleagues, The Sovini Group is a key contributor to the social, economic, and environmental development and future growth across the North West. To read more about The Sovini Group’s end-to-end supply chain services and Net Zero Carbon Commitment visit their website here.
Header image shows The Sovini Group’s Morris Meadows affordable housing development implementing offsite timber construction.