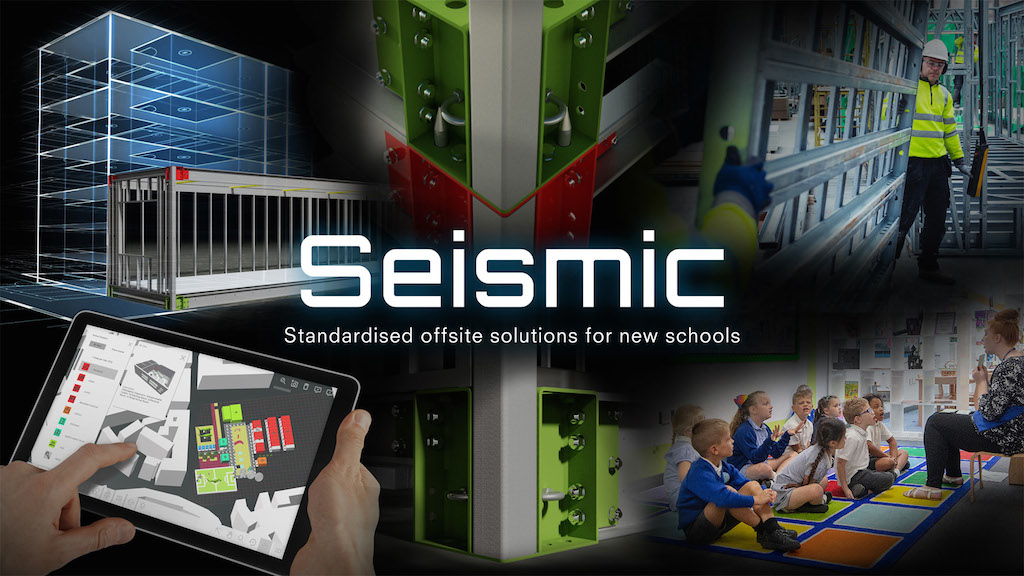
The results of a pioneering new consortium which set out to transform the way primary schools are designed, procured and built have been unveiled at a launch event in London and have been hailed as a trailblazer for transforming construction.
Two key innovations have now been unveiled by the Seismic Consortium – an innovative open source app for the design of primary schools and a universal connection solution and standardised structural frame for schools built offsite. The framing system has the potential to reduce carbon emissions for a typical 40-module school by 25%.
Funded by UK Research and Innovation (UKRI) through the Industrial Strategy Challenge Fund and Innovate UK, the Seismic Consortium comprises construction consultants blacc, the Manufacturing Technology Centre (MTC), technology-led design practice Bryden Wood and two of the UK’s leading offsite manufacturers, Elliott and The McAvoy Group.
The consortium was established to carry out extensive research and development into the increased use of standardisation to drive down costs, reduce lead times and radically improve productivity in the delivery of outstanding primary schools.
According to Sam Stacey, Challenge Director – Transforming Construction at UKRI, “The Seismic project is a powerful example that the targets set out in the Construction 2025 Strategy are achievable. It is one of the first Innovate UK projects under Transforming Construction to be completed and demonstrates that this level of collaboration is the future of construction.”
“This initiative has been a tremendous success and I am delighted to report that it has hit all of the targets for Transforming Construction. The project partners have demonstrated an unprecedented level of collaboration which we hope will inspire other forward-thinking projects to help innovate in construction and produce more efficient, sustainable and affordable buildings.”
“The focus of Seismic was to realise the Government’s ambition for greater productivity in construction and this has definitely been achieved with the offsite and digital solutions developed by the team. We are in no doubt that these innovations have the potential to change the way primary school projects are designed, procured and constructed, helping to meet the rising demand for school places and increase capacity in the construction industry.”
“The commitment, investment and R&D capabilities of each of the project partners has been very impressive and we are already realising the benefits in new Department for Education procurement frameworks. Seismic has shown how construction can be transformed and how by working together as an industry, even greater progress and innovation can be accomplished.”
The Seismic consortium has now launched:
• An innovative open source app that enables the full spectrum of community to get involved in the design of primary schools. The Seismic School app is a user-friendly, free web-based tool that has been developed to accelerate the initial design and feasibility stages for new primary schools. It will enable anyone from architects, planners, manufacturers to teaching professionals, school governors, parents and even pupils to configure a primary school building that will precisely meet their user needs on a specific site in full compliance with Department for Education and all regulatory requirements. The tool will significantly reduce the time and cost of the initial feasibility and design phases from weeks to minutes and will democratise the input of stakeholders by including them in the process. The app can be accessed at www.seismic-school-app.io.
• A universal connection solution and a standardised structural frame for school buildings built offsite. This advancement in offsite manufacturing significantly reduces components and removes the need for welded joints, reducing labour costs and improving efficiency in a production environment.
Research carried out by the consortium has demonstrated that by rationalising the design of the steel structure, the amount of steel used in an average primary school built offsite can be reduced by 25%.
This generates a cost saving of up to 25% for the modular steel structure and carbon emissions for a typical 40-module school are 25% lower — equivalent to over 155,000 miles of car driving or 17 flights from London to Sydney.
The team is in the process of finalising testing for the new framing solution and is collaborating with steel fabricators to develop the standardised components and establish a supply chain with a view to making these available to the offsite market in the coming months. This will aggregate demand and allow significant economies of scale to drive down costs.
The consortium has aspirations to apply the same manufacturing principles to ‘componentise’ other parts of a building to be able to offer a whole school solution, including walls and roofs. It also aims to develop a ‘product family’ for different types of buildings, such as housing and healthcare, acting as a catalyst for revolutionising the wider construction industry.