John Mellor from Glidevale Protect explains how adopting a fabric first approach and drawing on specialist hidden protectors in the building envelope can further enhance the benefits of offsite to create buildings that can help contribute to low operational carbon, deliver condensation control and stand the test of time.
With the onset of climate change and reduction of carbon emissions in construction becoming mandatory with more demanding energy efficiency requirements set down in Building Regulations Approved Document L, and with the Future Homes Standard 2025 edging ever closer, many developers for local authority projects are now utilising offsite construction as a way to create energy-efficient buildings not just in homes but also in workplaces, schools, hospitals, leisure facilities and other commercial buildings.
Hidden protectors provide the perfect balance
In order to meet new demanding energy efficiency targets, a building’s construction should combine both a thermally efficient and airtight solution — and the factory-controlled, precision manufacturing environment afforded by offsite helps to minimise the performance gap between how a building was designed versus in practice.
While a measure of airtightness and thermal efficiency is essential when assessing the energy efficiency of a building, it’s crucial to balance this against ventilation and condensation control at the same time. Hidden protectors can come into their own on a project, this includes the use of floor, wall and ceiling membranes which can aid thermal efficiency yet ensure condensation risk is managed effectively.
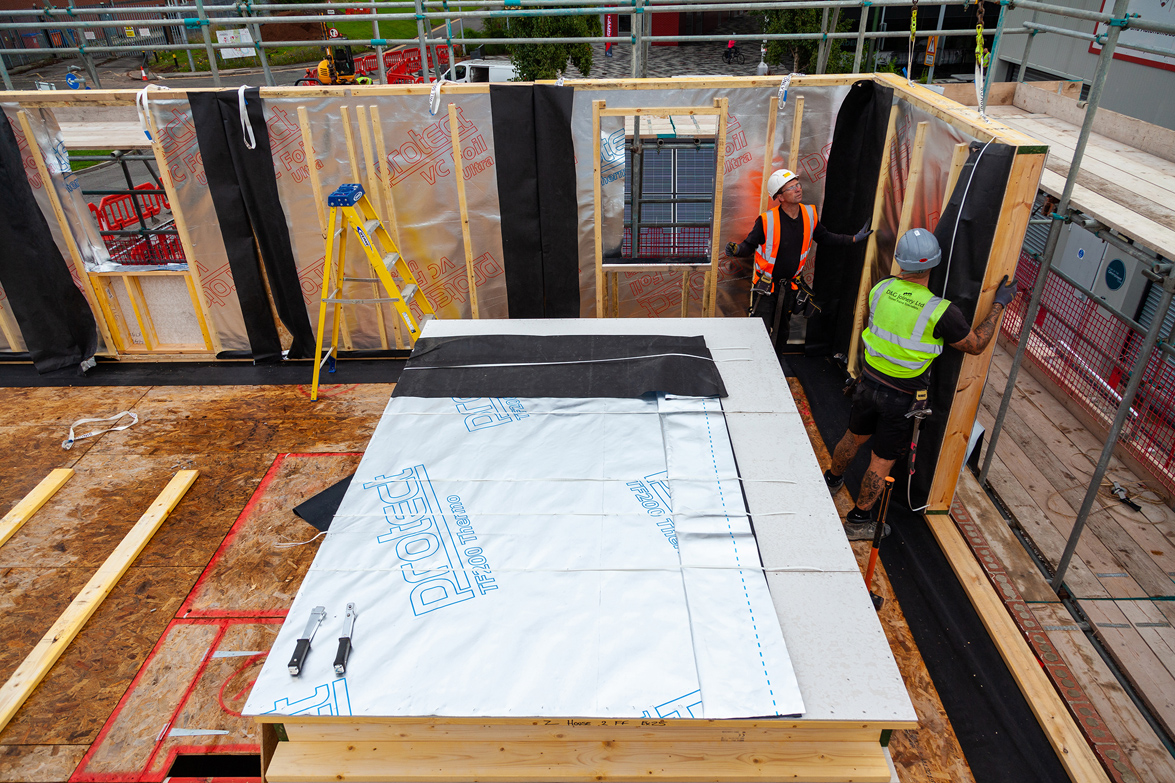
Specifying products as a system rather than on an individual basis can be beneficial to ensure elements of the building fabric work together harmoniously. For example, Glidevale Protect recommends the use of three reflective, low emissivity and insulating construction membranes used together within a timber frame wall panel construction to maximise energy efficiency of the fabric.
This system of membranes includes Protect TF200 Thermo or Protect Thermo Extreme, installed as the external breather membrane on the cold side of the insulation, with Protect TF InterFoil within the timber frame stud facing into a still airspace and Protect VC Foil Ultra installed within a service void on the warm side of the insulation. This can generate potential insulation cost savings, whilst achieving low U-values and can ensure the wall’s footprint is not increased.
When using Glidevale Protect reflective membrane technology, the high purity, solid aluminium foil ensures the membrane forms a radiant barrier when the foil surface is facing at least a 20mm unventilated airspace within a wall construction. This creates a low emissivity cavity, which significantly reduces heat loss and raises the thermal resistance of the airspace. The correct use of internal and external reflective membranes will effectively block infrared radiation and increase the thermal performance of the airspace, allowing low target U-values to be met.
Such specialist membranes are ideal for direct delivery in bulk to the factories within the offsite construction sector to ensure ease of installation within the factory, which in itself can help reduce the environmental impact and carbon emissions of developments, helping the manufacturer deliver more pre-manufactured value (PMV).
Tomorrow’s World — delivering next generation buildings today
As well as focusing on the fabric of a building to contribute to its overall energy efficiency and help reduce fuel bills associated with heating and cooling, additional elements can be included in addition to hidden protectors, which will bolster the performance even further. These innovations are particularly effective when they can be integrated easily with offsite construction.
For example, Manchester company, Discrete Heat Co Ltd’s innovative new heated skirting board system, ThermaSkirt, removes the need for traditional wall-mounted radiator systems to heat rooms effectively and is an ideal fit within offsite factory construction such as volumetric modular. Tests have shown that when combined with Glidevale Protect’s VC Foil Ultra reflective air and vapour control wall membrane, the radiated heat provided evenly and efficiently around a room by ThermaSkirt is enhanced with increased temperature levels by at least three degrees centigrade — thus reducing overall energy consumption.
By offering a tailored consultancy service for offsite manufacturers, as well as providing technical support services such as airflow calculations, thermal modelling, U-value calculations, condensation risk analysis and optimising materials delivery direct into offsite factories, Glidevale Protect can support the offsite construction sector to ensure transparency and traceability of material specification.
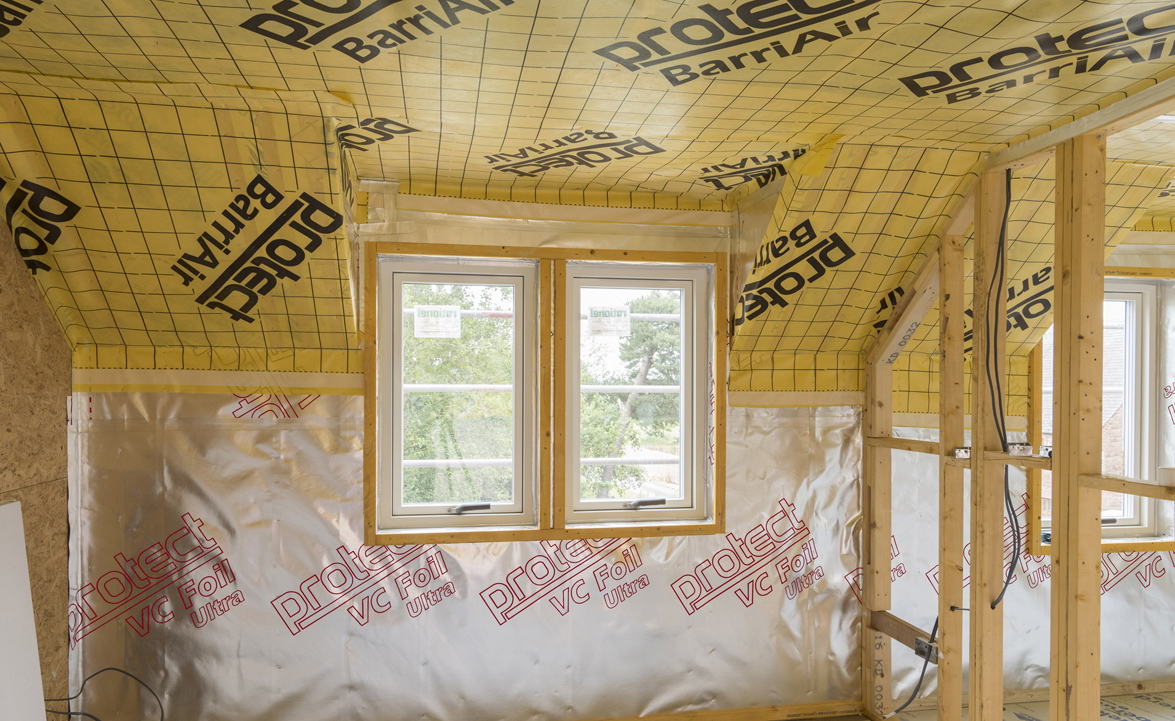
With the golden thread of information in offsite construction of paramount importance and the sustainability of any project relying on the performance of individual products specified, it’s essential that technical data can be relied upon to achieve full compliance. Glidevale Protect can support this with individual BIM Objects available via NBS Source and BIM Store, as well as fully backed up, independent product certification.
In addition, product and factory specific Environmental Product Declarations (EPDs) are also available for Glidevale Protect’s key construction membranes, in accordance with EN 15804 and ISO 14025, providing clear sustainability and life cycle assessment data. Determining a product’s global warming potential helps those in offsite construction sector gain an insight into the environmental footprint of the materials being used for installation.
As the drive to meet net zero targets continues, hidden protectors in the form of construction membranes can make an added contribution to the energy efficiency rating of a building and help maximise the benefits and PMV value of offsite construction.
Header image: Protect TF200 Thermo membrane installation to timber frame panels.