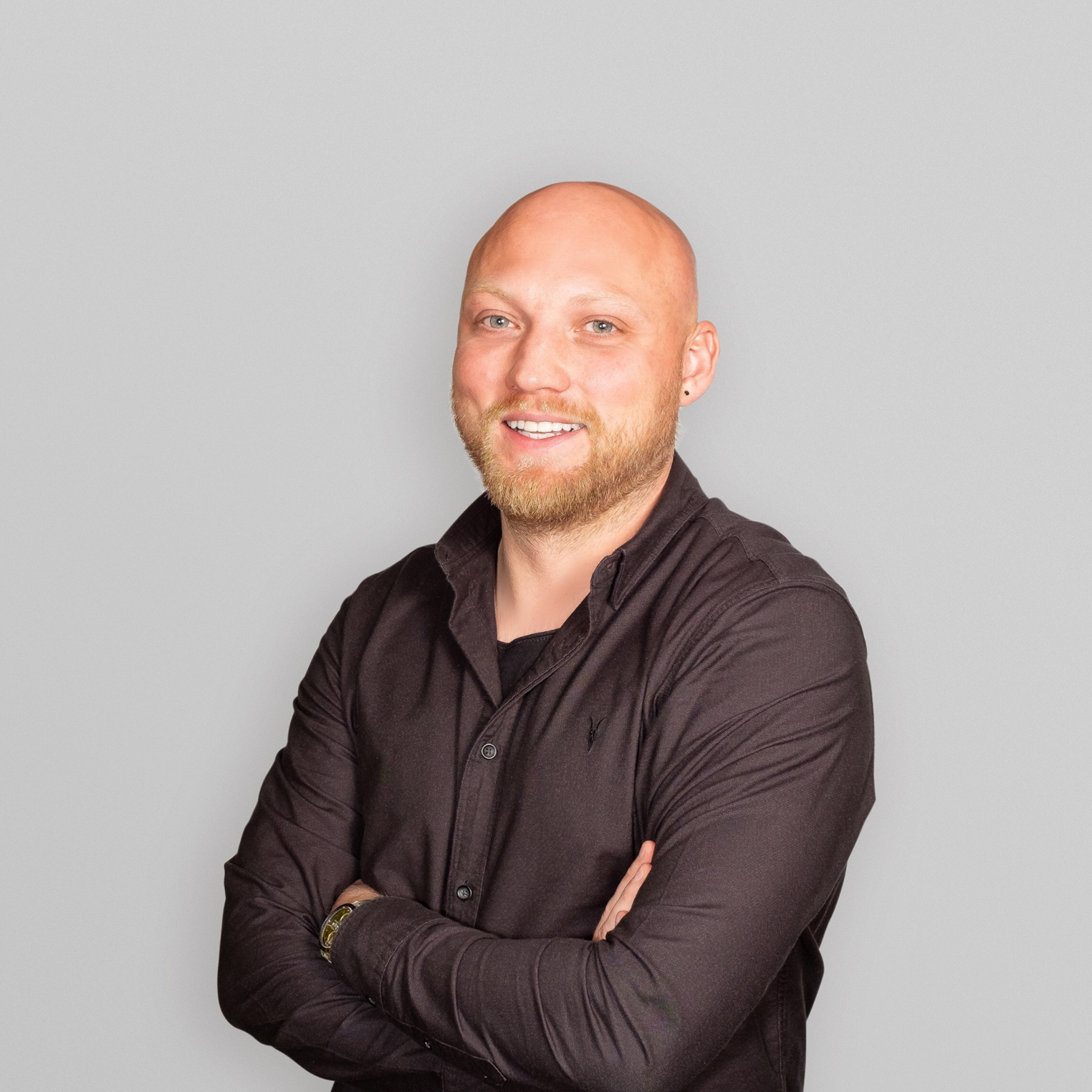
With a national housing shortage and ambitious housebuilding targets for developers and local councils to meet, is now really the time to put the pressure on the industry to explore more sustainable methods of construction? The answer is a very clear yes from Wayne Oakes, a Director at the sustainable engineering consultancy, Dice. He believes a greener modular building approach can increase sustainability, reduce construction time and begin to tackle the huge volumes of waste generated by the construction industry.
The UK’s housing crisis is well documented, with ambitious targets set by the Government of 300,000 new homes a year. With that comes a secondary problem, that of construction waste. A DEFRA report highlighted that in 2018, construction, demolition and excavation accounted for 62% of the UK’s total waste.
So how do developers continue to build at speed, reduce the volume of waste materials and create more sustainable methods of construction? The answer is staring us all in the face — modular homes.
Modular homes are designed to be energy-efficient and very efficient to manufacture. They’re created offsite — where waste can be kept to a minimum — and different elements of a build can all be happening at the same time.
Offsite construction enables phases of work to be undertaken concurrently. Onsite substructure and infrastructure work can be taking place whilst the superstructure is being built in a factory. Factory conditions also mean that there are no delays due to inclement weather.
And there are environmental benefits to working offsite, helping us to fight the climate crisis. It is more straightforward to manage waste in a factory environment rather than on a construction site. It allows for far more control meaning less contamination, more recycling and less overall waste.
Another large contributor to climate change is pollution and energy output. Modular designs see a 40% reduction in HGV movement at construction sites, and manufacturing offsite also minimises the time and energy spent on site. This cuts travel and transport, as workers are more likely to be concentrated around a specific factory. Due to these factors, overall pollution is reduced.
Recycling is another big focus across every sector. Materials in traditional construction like timber, brick and concrete, are very rarely re-used and it can be hard work to do so. The volumetric and panelised systems found in modular building lend themselves to recycling in a much more practical and efficient way.
There are challenges, as there are with every construction project, and they do require a different approach to traditional methods of construction. Modular projects and units do differ from the traditional, standard residential units. They have specific requirements in terms of their sub-structures and external works. This is particularly the case in sites with gradients and water management requirements.
On our first modular project, we worked very closely with the manufacturer on specific design standards, in particular with regards to the National Housebuilding Council’s requirements for the substructure. This was a condition of the offsite manufacturing partner, to ensure that each of the plots met the requirements of building control.
As engineers, we need to be agile, responsive to site specific needs and challenge design to ensure modular methods of construction get the recognition they deserve. We’ve realised technology’s potential and are driving the change. It’s our duty to think creatively to develop new, more sustainable ways of construction and ultimately living.