Ian Thomas, Product Manager – LabControls at TROX UK, offers advice on air management strategies and tackling laboratory energy costs.
The current energy crisis is of particular concern for sites incorporating facilities for scientific testing and teaching. The energy consumption of laboratories is often more than three or four times that of offices on a square metre basis.(1) This can mean that laboratory buildings are responsible for between 50 and 80% of the total energy-related (non-residential) carbon emissions of research-intensive universities.
Government research facilities, hospitals and private sector laboratories are similarly affected, with energy consumption presenting significant financial and environmental challenges. There are a number of measures that can be taken, however, to reduce laboratory energy consumption without compromising health and safety, or the integrity of research.
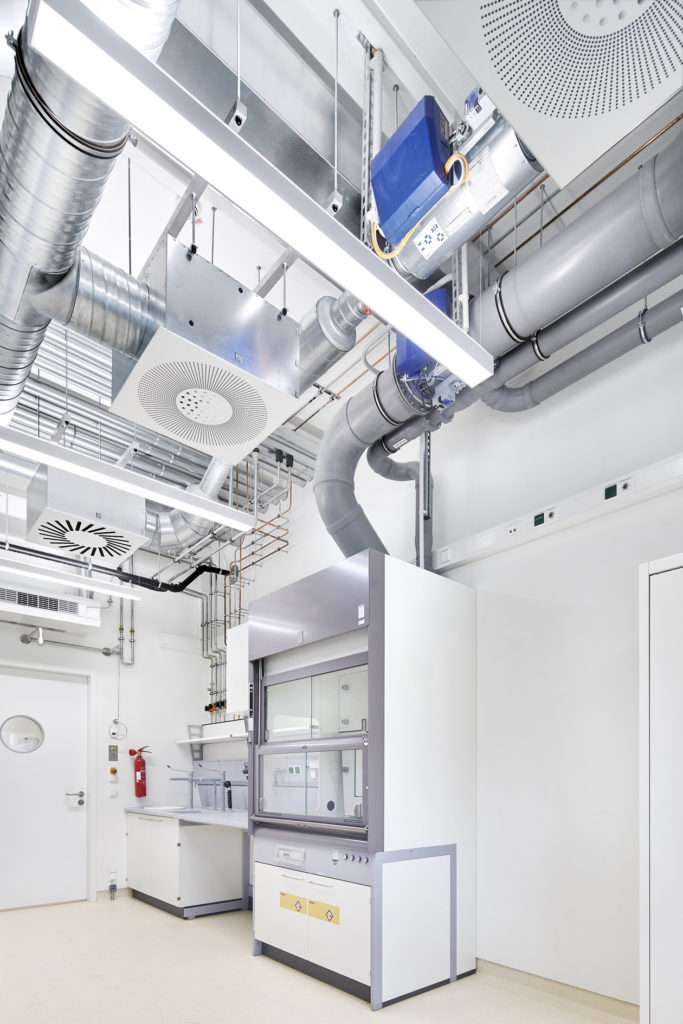
Step 1: Review existing air management strategies
An understanding of existing air supply and extraction across the site will provide a firm foundation for any energy-saving project. Often air change rates are set on a site-wide basis. This can result in higher air change rates necessary for laboratories being applied in areas used for administration, meetings or general teaching. Accurate zoning could mean that air change rates could be reduced safely in low risk areas of the site to reduce the site’s overall energy consumption.
A sensible next step is to analyse air change rates in the laboratory areas at the weekend, or overnight, at times when these facilities are unoccupied. Expert advice is, of course, recommended, but there may be valuable opportunities to adjust the BMS to reduce air change rates for the air conditioning systems at times of non-occupation. Local overrides can be used to ensure that, if personnel should be working out of usual work hours, the air changes can be re-established at times when the BMS has put the building into reduced mode.
Step 2: Identifying major energy-consuming devices
The higher energy consumption of laboratories is driven largely by the use of fume cupboards. A 900mm wide fume cupboard with a maximum sash height of 500mm and face velocity of 0.5 m/s would extract approximately 225 l/s of conditioned air from the room. This higher than average demand for conditioned air has a significant knock-on effect across the site, driving up the energy consumption of air conditioning system components such as Air Handling Units, chillers and fans.
The energy consumption of the fume cupboard is dependent largely on whether it operates on constant or variable air volumes (VAV). A VAV fume cupboard reduces extraction automatically when the sash is closed. For the example above, this figure drops from 225 l/s to just 55 l/s when the sash is down, reducing the conditioned air requirement by 170 l/s. So transitioning older fume cupboards from constant to variable air volume has significant energy saving potential.
Relatively minor changes to day-to-day operation of VAV fume cupboards could also unlock significant energy savings. Sashes are often left open when individuals are away from the fume cupboards, resulting in unnecessary consumption of conditioned air. It is a relatively simple operation to install technology to close sashes automatically to conserve energy.
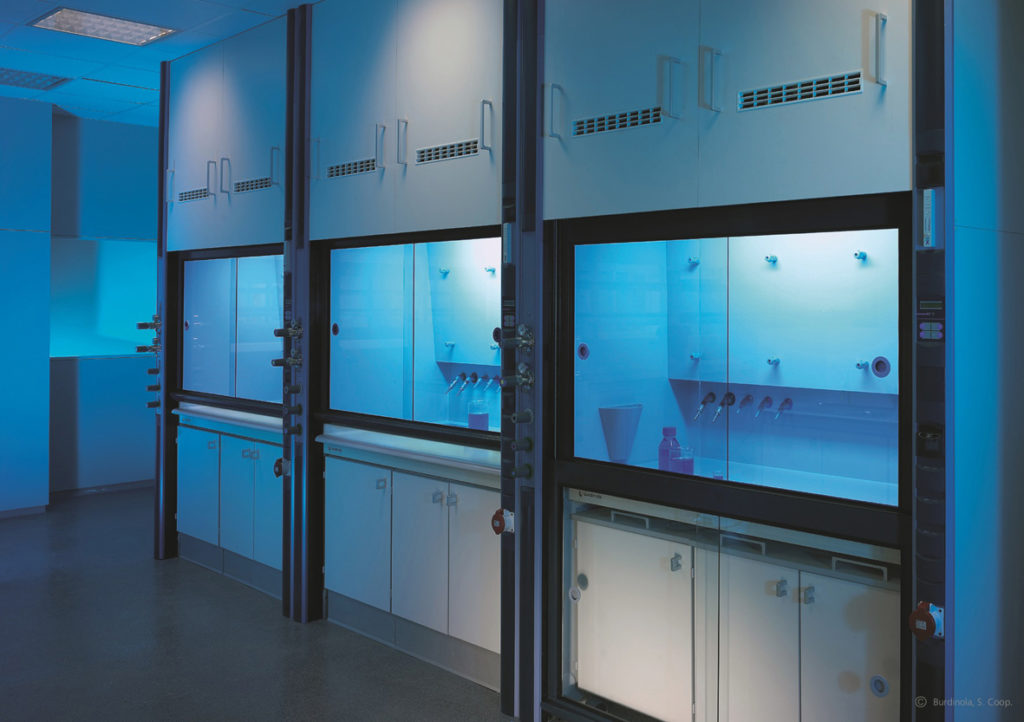
A PIR (passive infrared) sensor can identify that no one is present at the fume cupboard. After a set time a visual or audible alarm is triggered to indicate that the sash have been left up. An auto sash closer can then work in conjunction with the sensor to close the sash automatically, preventing unnecessary extraction of conditioned air.
Further energy savings could also be possible by upgrading or reactivating control features of the existing fume cupboards. It is quite common for fume cupboards to have control capability already resident but not currently configured for operation. Existing features could be brought into operation, or more advanced control could be retrofitted to the existing lab ‘hardware’ to maximise return on capital investment whilst providing new energy efficiency and safety capabilities.
Step 3: Room air management
The most significant energy reductions, however, can be achieved by integrating fume cupboard air supply and extraction with the wider air management systems to prevent wastage. Installing a room air management system (such as the TROX EASYLAB system) makes it possible for all input and extract air for the laboratory to be controlled automatically to ensure that the required ventilation strategy and levels of safety are maintained.
Supply and extraction of the fume cupboards (or other technical air management devices) is automatically balanced and offset in line with changing requirements, reducing the total supply and extract volumes. For example, if the fume cupboards are open and extracting air, there is not the same requirement for the room system to carry out this process. By scaling down room exhaust air extraction in line with fume cupboard extraction, the room air management system is able to prevent wastage associated with over-supply of conditioned air, improving energy efficiency significantly (see Figures 1 and 2 above).
Step 4: Local heat extraction
Finally, installing equipment such as ventilated down flow tables, canopy hoods or fume exhaust ‘snorkels’ can take away heat at source, thereby reducing demand on the site-wide cooling and ventilation system. These can be particularly helpful where cooling demand relates to intensive usage of IT equipment on laboratory benches.
1. Peter James and Lisa Hopkinson, ‘Carbon, Energy and Environmental Issues Affecting Laboratories in Higher Education — A Supplement to the HEEPI Report on General Regulations and Schemes on the Topic’, August 2011.