Steve Hill, National Sales Manager for UK home lift manufacturer, Terry Lifts explains the importance of stable supply chain partnerships during these challenging times, and why there is no room for compromise when it comes to selecting a home lift supplier.
As another challenging year ends attention turns to the new financial year and budgets. While there may be some areas where cuts can be made (yes, further still), there are others where the impact on resident welfare is just too great. One such area is improved access to rooms, facilities, or gardens, for example with a home, step or platform lift.
We work with many local authorities supporting vulnerable and elderly residents with home access solutions. While some residents in England, Wales, and Northern Ireland may gain financial support through a Disabled Facilities Grant, that’s not always the case.
We fear that as the stranglehold on council spending grows ever tighter, efficiencies may put residents at greater risk. To prevent this we are encouraging procurement, facilities and maintenance teams to pay close attention to the standards and professionalism of their chosen home lift supplier and their products. Investing in a high quality and reliable lift from a proven and trusted supplier will be more cost-effective in the long run.
Stable supply chain partner
Firstly, consider the supply chain, is it stable? Is the lift manufactured in Britain? Where are the components manufactured? How does the lift company manage its supply chain? These are all valid and important questions.
The pandemic exposed the vulnerability of some UK lift companies, those whose products are shipped in from abroad. Delays and soaring shipping costs hit hard. With end-users feeling the brunt.
A UK supply chain makes problem solving easier. Over the years we have received numerous requests and questions. Sometimes this sparks an idea for a tweak or development to an existing product. And because our suppliers are on our doorstep, we can react to this, quickly. It’s the same if there is ever an issue, we can act fast and remedy it. There’s no waiting for weeks while the solution crosses the water.
Made in Britain
Our supply chain is huge. We use between 50-60 suppliers regularly and utilise almost every part of British manufacturing, from electronics and hydraulics to fabrication, turning, pressing, and punching to name a few. We are incredibly proud to support British talent. This is one of the reasons we applied to be Made in Britain accredited.
As a Made in Britain member, customers recognise that Terry Lifts products are British-made and are manufactured to the highest standards. The mark promotes trust and confidence.
On awarding the accreditation Made in Britain CEO, John Pearce said: “Terry Lifts epitomises the innovation, consistency and resilience that are embedded in the DNA of the British manufacturing sector. Terry Lifts’ existing and potential customers can clearly see that the company’s products adhere to the highest standards and are of truly British provenance.”
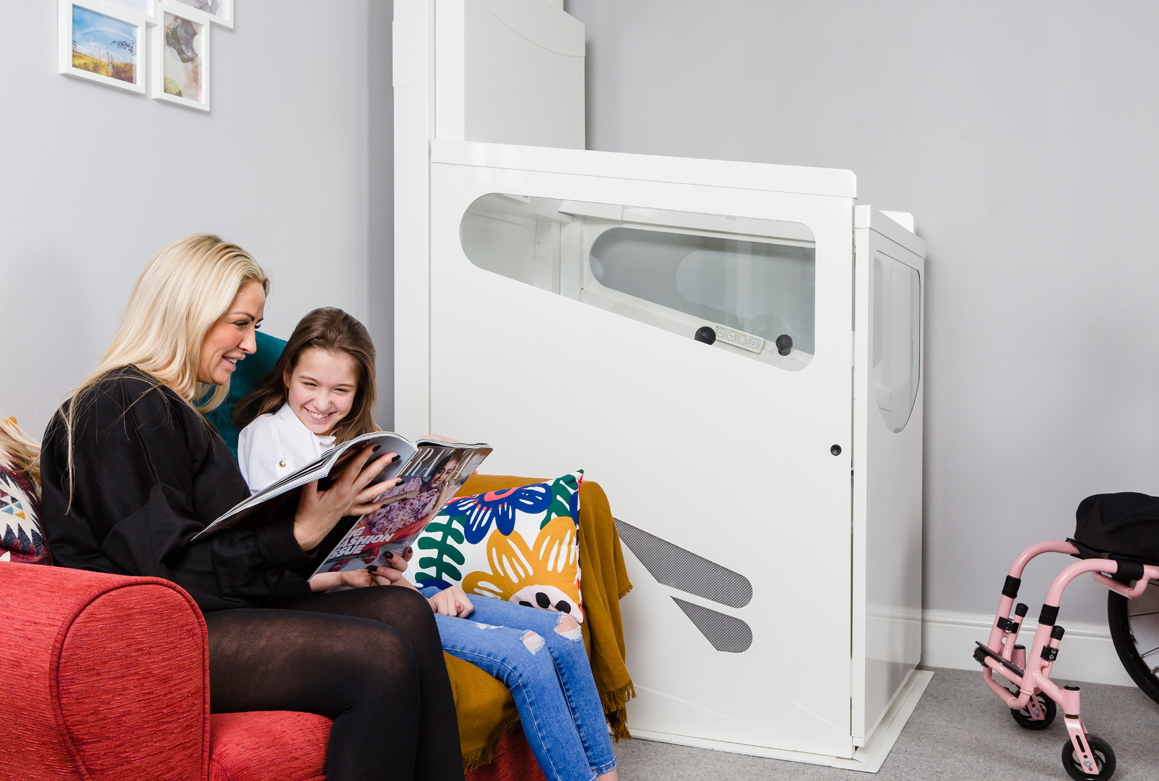
Quality and compliance
Then of course, there’s the question of quality. Divergences in global standards can lead to quality and reliability issues. Lifts manufactured here in Britain are subject to British and European standards, and are produced by trained, skilled engineers. This isn’t the case for every home lift supplier currently selling products in the UK.
A through-floor home lift should comply with the Machinery Directive 2006/42/EC. But, perhaps, more important, is compliance with the requirements of BS 5900:2012.
A through the floor lift requires an opening to be created for the lift to pass through when travelling from floor to floor. This instantly breaks the fire integrity and removes the fire protection of the first-floor structure — potentially enabling a fire to move freely between floors.
To minimise risk, it is vital that an independently certificated through the floor lift is specified. Look for a product that complies with BS 5900:2012 (Powered home lifts with partially enclosed carriers and no lift way enclosures) and is independently tested by an approved Notified Body. A compliant product will maintain the fire and smoke protection between floors, whether it is parked upstairs or downstairs.
British-based expertise
Underpinning this is access to help and expertise, locally. Whether that’s via an approved and trusted network of agents and partners or in-house advisors. With a British manufacturer there’s often an expert in each area of the business including design, manufacture and installation, individuals who can offer guidance and support throughout the procurement process and beyond.
After-sales care and support are vital when appointing a lift access provider. Some lift suppliers also offer training, sharing their expertise with facilities managers and maintenance teams, amongst others, allowing for repair and maintenance to be carried out to a professional and approved standard.