Jon Lane, Commercial Director at Taylor Lane Timber Frame and member of the company’s Corporate Social Responsibility Committee explores the impact of the energy crisis and how changing our housebuilding methods will help to deliver high quality, energy-efficient homes.
The current UK energy crisis is unprecedented. On the 8th September the Government announced a plan to freeze household energy bills at £2,500 a year on average for the next two years from 1st October. While this will go some way to alleviate the pressure on UK households, the national fuel poverty charity, National Energy Action (NEA) has estimated that ‘6.7 million households would be fuel poor…’. That’s up from 4.5 million in fuel poverty last October. ‘The number of households in fuel poverty remains high, despite a raft of [government] measures…’
‘Across the UK, cold homes are already damaging the lives of the poorest households.’ NEA goes onto suggest ‘…the UK Government should plan to provide lasting support for households, instead of relying on a series of ‘one-off’ measures.’ Amongst their solutions, NEA suggests ‘Setting tighter regulatory minimum efficiency standards for rented properties, so that they reach EPC C by 2030 at the latest.’
This approach would complement the UK’s legally binding net zero target by 2050. While the measures by which this will be achieved have been legally challenged in the high court by environmental groups, the strategy remains government policy (at the time of writing).
As a timber frame manufacturer, we have already pledged our commitment to become a net zero company, joining the Greener Footprint ‘30 for 2030’ campaign, launched earlier this year by the Herefordshire Climate and Nature Action Partnership.
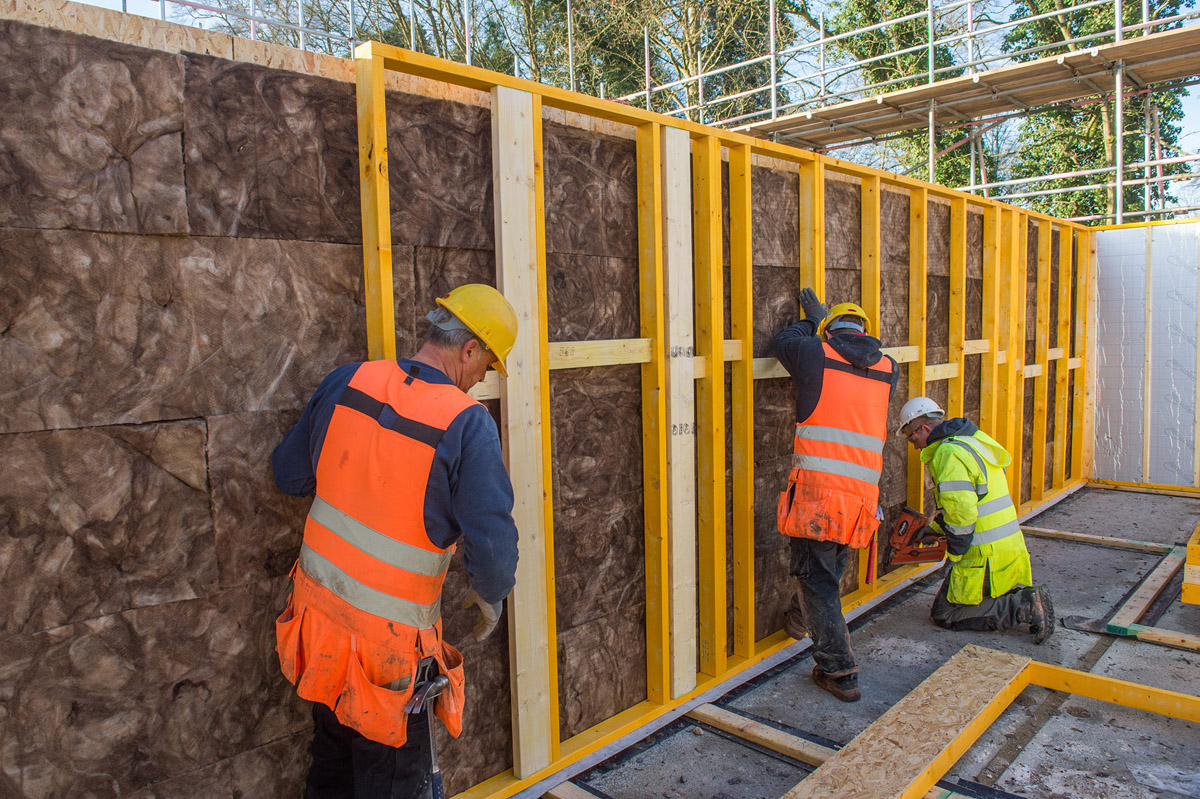
Inefficient housing
While the energy crisis is unprecedented, it is simply exacerbating existing societal, economic and environmental issues — such as the need to invest in energy efficient measures to bring people’s homes up to standard.
A recent study by Friends of the Earth, discussed in an article written by Energy Correspondent Alex Lawson on The Guardian’s website in August, analysed 30 local authority jurisdictions and identified ‘…nearly 9,000 “hotspots” across England and Wales where energy use is high and typical household income is below the national average. […] The study found that 65% of Birmingham’s neighbourhoods faced hardship related to energy bills. Households can also suffer higher power costs due to poor insulation and the study found that 59,410 homes in Birmingham needed loft insulation. More than 47,000 did not have cavity wall insulation.’
While we agree that energy-efficient measures such as cavity wall and loft insulation would be beneficial for poor performing housing stock, we must act now to ensure that history doesn’t repeat itself with new-build houses. They must perform better, and in turn be affordable, comfortable and healthier homes. This starts with the fabric of the building.
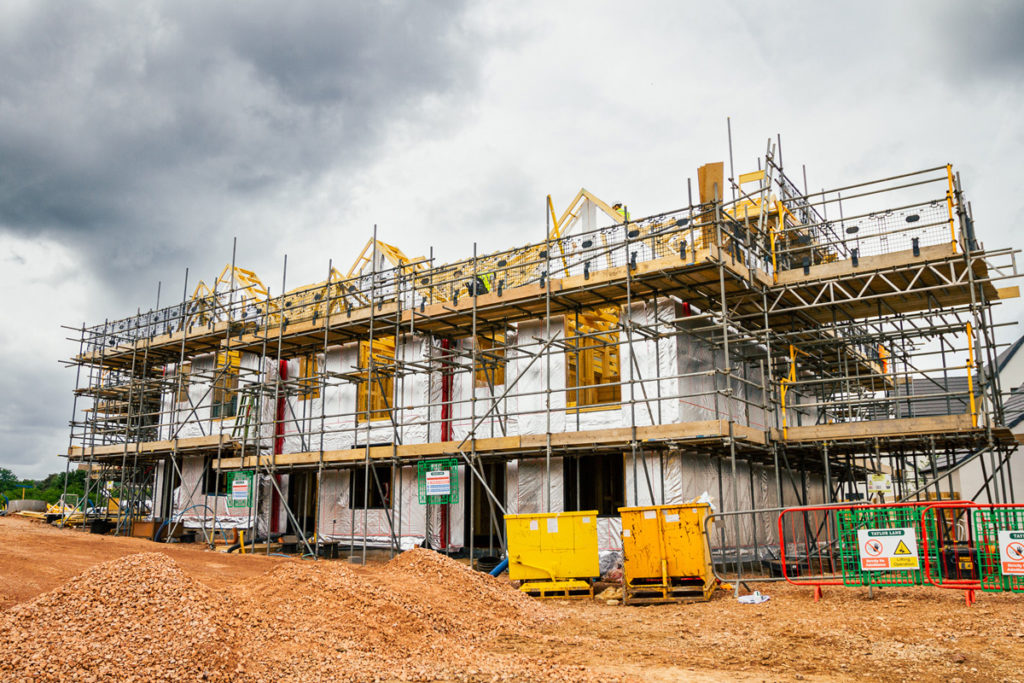
Benefits of timber frame
Timber frame is generally considered to be the most environmentally friendly building material when compared to brick, steel and concrete; it has the lowest energy consumption and carbon dioxide emissions.
It is therefore unsurprising that timber frame construction is fast becoming a build method of choice for local authorities and housing associations. Popular for the speed of construction, contractors, buyers and specifiers are now also appreciating its green credentials too.
CO2 savings
Wood products are low carbon materials. They can help reduce CO2 in the atmosphere and help slow climate change. For every cubic metre of wood used instead of other building materials, 0.8 tonne of CO2 is saved from the atmosphere.
A typical 100m2, two-storey detached timber frame home contains 5-6 cubic metres more wood than the equivalent home built using traditional build methods such as brick and block.
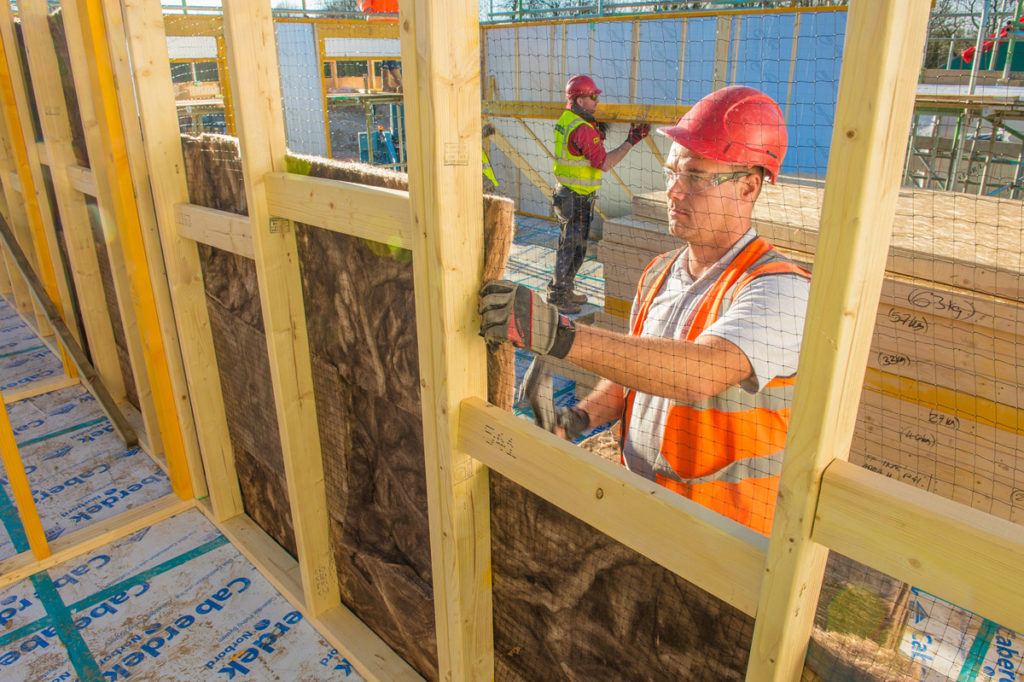
Carbon capture
Trees capture harmful CO2 from the atmosphere and store it as carbon. When harvested, that wood is used for products such as timber frame components, and those products store carbon for that product’s entire lifecycle. After being harvested, we plant more trees, and the cycle of capturing CO2 continues (for more information visit woodforgood.com).
The sustainable option
As a Structural Timber Association (STA) Assure Gold member, we encourage the use of timber from PEFC or FSC certified sources. Buyers and procurement teams must look out for FSC, PEFC, SFI, CSA and MTCC certified sources. A reputable timber supplier should also provide a full chain of custody.
Energy savings
Now this is where timber frame comes into its own. As a natural insulator, timber, when used as a build method, can help to reduce running costs and energy bills. A property will remain warmer throughout the winter and stay cooler during the summer months. It can heat up quickly and retain that heat for longer.
It is far easier to achieve a low U-value with timber frame than traditional build methods. It goes beyond Building Regulation requirements without filling the cavity.