When there’s a need for speed, having a UK-based manufacturer can help with quicker delivery times. Saint-Gobain Weber has three manufacturing plants within the UK — Bedfordshire, Shropshire and County Antrim. From flooring products to external wall insulation (EWI) systems, the company shares with LABM how it has played an important part in making sure multiple hospital projects are delivered on time.
When the operating theatres at the Royal Hallamshire Hospital were being refurbished, the hospital was still in use throughout the project. Henry Boot Construction, the main contractor on the project, approached resin floor and concrete repair specialists Frescrete to prepare and install new floors.
Frescrete worked within strict hospital guidelines and to the contractor’s tight timescale of 72 hours to minimise disruption. This meant deliveries were arriving throughout the night, enabling work to commence early in the morning.
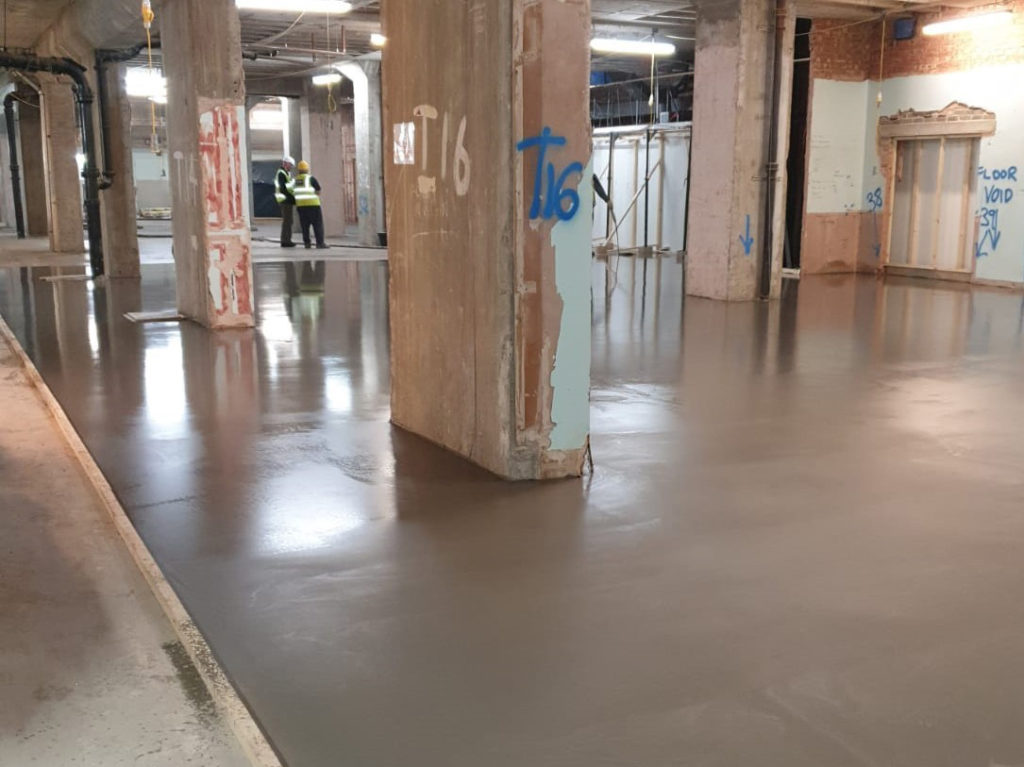
A smooth finish
The floor had to meet surface regularity one (SR1) levels of flatness, and with a fixed timeframe to prime and install the floor with no room for error, Frescrete turned to Weber.
“Frescrete were very clear about what they needed from the screed; ease of application and fast drying time,” said Andrew Cooper, Regional Specification Manager for flooring at Saint-Gobain Weber. “We specified weberfloor 4716 primer and weberfloor smooth rapid 4160 as both have fast drying properties. The weberfloor smooth rapid 4160 was ideal for this project as it can withstand light foot traffic after just a few hours and the final floor covering can be installed after 24 hours.”
As this was Frescrete’s first time working with Weber’s flooring products, Kevin Grainger, Applications Manager at Saint-Gobain Weber, worked alongside the company to provide technical support. “We primed the substrate within a day, applied the screed within 24 hours, and by the third day it was ready to have the vinyl covering fitted. Three days to install 600m2 of flooring to precise levels of flatness is impressive,” said Joshua McKinlay, Contracts Manager at Frescrete.
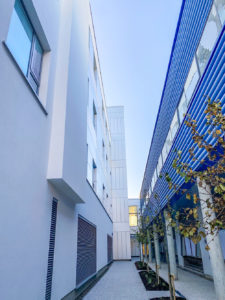
In times of emergency
A new 60-bed ward block at University Hospital Limerick was built at the start of the Covid-19 pandemic despite both the UK and Ireland being in lockdown. The Health Service Executive had been planning to upgrade and replace old ward blocks that were originally constructed in 1955 and to expand the number of beds at the hospital, when the Covid-19 pandemic struck.
The need to increase capacity at the hospital became even more urgent as the existing facilities were not suitable for the volume of patients that were expected nor for minimising the risk of spreading the virus.
Modular build
Architects O’Briain Beary designed the new block using a conventionally built ground floor plant room as the base. A rapid build, modularised steel frame system (SFS) was then erected above the plant room to form a three-storey block, with three inpatient wards of 20 ensuite rooms which would help staff to isolate patients and improve infection control capabilities.
Once the steel frame was erected and cement board installed, the modular design specified an efficient, certified External Wall Insulation (EWI) system that met all stringent safety standards.
Weber’s webertherm XM was identified as one of the only systems available that fulfilled the requirements. EWI systems have huge thermal benefits for any building by conserving energy, minimising heat loss and reducing CO2 emissions. In addition to this, having a fully certified non-combustible solution offers great peace of mind, as well as a fast-track way to provide an attractive and durable façade.
However, as the UK and Ireland were in lockdown, Weber’s offices and manufacturing facilities were shut down. Shane Kehoe, Weber’s Sales Manager for Ireland, was contacted by the Health Service Executive who confirmed that the project was considered essential work and as such, operations to supply materials could continue.
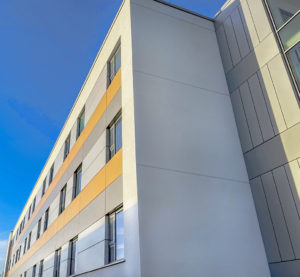
at Limerick Hospital. ©Clarke ECO Wall Ltd
“The problem was that one of our raw material suppliers was operating with a skeleton staff and had reduced their service making it difficult to deliver materials to site,” explained Shane. “After meetings at board level between contractors and raw material suppliers, we were able to put in place a production schedule to meet the fast-track timetable for this urgent project. It was a real team effort between
myself, Alan Burnell — the Specifications Manager for Ireland — and other members of Weber’s Ireland-based team.”
Clarke ECO Wall Ltd, a render and EWI specialist, was enlisted to install the EWI system for the 1,300sqm project, which was supplied through Murdock Builders Merchants.
The system included 160mm webertherm MFD mineral fibre insulation board to achieve a U-value of 0.14W/m2K, followed by weberend LAC rapid, and then webersil TF, a highly weather-resistant silicone decorative finish in Chalk.
Weber’s team made weekly site visits to support the applicators to ensure the system was installed in line with Weber’s recommended best practice. The project was completed in just 16 weeks with the first ward opening in November 2020 to enable Limerick Hospital to provide critical services to the surrounding community during the pandemic.
Header image: Royal Hallamshire Hospital. Photo courtesy of Gilling Dod Architects