The Off-Site Homes Alliance (OSHA) talks to LABM about unlocking the benefits of modular for social housing through collaboration.
According to recent research by Shelter, the UK needs to build at least 340,000 homes per year — and of that at least 150,000 good quality affordable homes in order to address a shortage of homes, yet the average annual output continues to be below that figure.
With the social housing sector continuing to face a range of challenges, this has highlighted the important role that innovation in project delivery will play in boosting current productivity levels. It has also been a key factor in the increased attention from social housing providers in the adoption of Modern Methods of Construction (MMC) in their acceleration strategies to deliver high-quality affordable homes, as Mike Ormesher, Project Director at the Off-Site Homes Alliance (OSHA) explained: “The benefits of MMC has been very well documented, helping to speed up the delivery of social housing in communities where they are most needed.
“The approach to OSHA has been quite astonishing, as social housing providers (RPs and LAs) approach us to deliver MMC homes that meet new performance and high-quality standards and of course, affordability.”
Addressing the housing shortage
Mike continued: “The industry now widely accepts that the use of MMC technologies is key to addressing the housing shortage and performance challenges, as a completely joined-up strategy. It’s a view also supported by Homes England, making commitment to increased use a key prerequisite for its strategic partners. MMC are now the new norm as we drive up standards towards zero energy bills and zero carbon footprint ambitions.
“We’ve been using MMC for decades. Our first recorded volumetric houses (Henry Manning Modular Cottages) were being shipped from Great Britain to Australia as far back as 1827 in timber frame. The real contrast today that differentiates “the old” from “the new” MMC philosophy is that we are now ‘designing in’ real performance, sound value engineering, significant safety, and robust compliance measures at every stage.
“We’ve drastically improved our DfMA processes for integrating MMC technologies into the actual construction delivery process too. The compliance measures and processes we now have for MMC systems (e.g. working with strategic partners such as NHBC Accepts, BOPAS
and numerous others now well founded for MMC management) are far more robust than ever before.
“The approaches we now follow, are far more appropriate for testing too, rather than trying to test hundreds if not thousands of individual components separately, in the hope that they all work together on the end product (our homes).
It is also far easier for the more advanced accreditation, certification and ultimately MMC warranty bodies, to build in QA procedures, roles and responsibility insight, management processes, skills, training records, system design and installation manuals, material schedules, testing
records and drawing control etc, as part of the MMC delivery process ensuring better securitisation and asset management. This is due to the holistic approaches now afforded using MMC philosophy.”
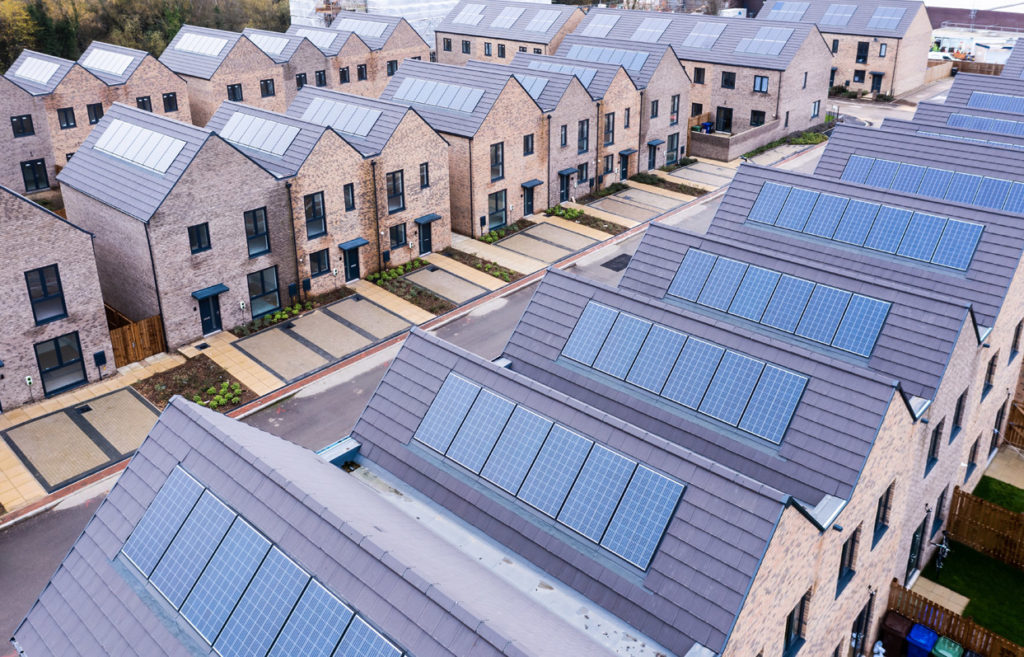
Future of construction
As we require more consumer insight and control to manage energy, wellbeing, comfort levels and certainly safety levels, and as we start to reach our target dates for future homes and zero carbon, the use of MMC has never been more aligned and is without doubt the future of construction across the board.
We should start thinking, control over production, available insight into the end product, and ease of management for transparent compliance procedures. Then MMC means something. This is what OSHA has taken on as part of its well-established and defined strategic management
process or MMC Eco-system as its now known to its clients and strategic partners, overcoming any hurdles that do or may exist in the MMC delivery programmes, now being managed for its clients.
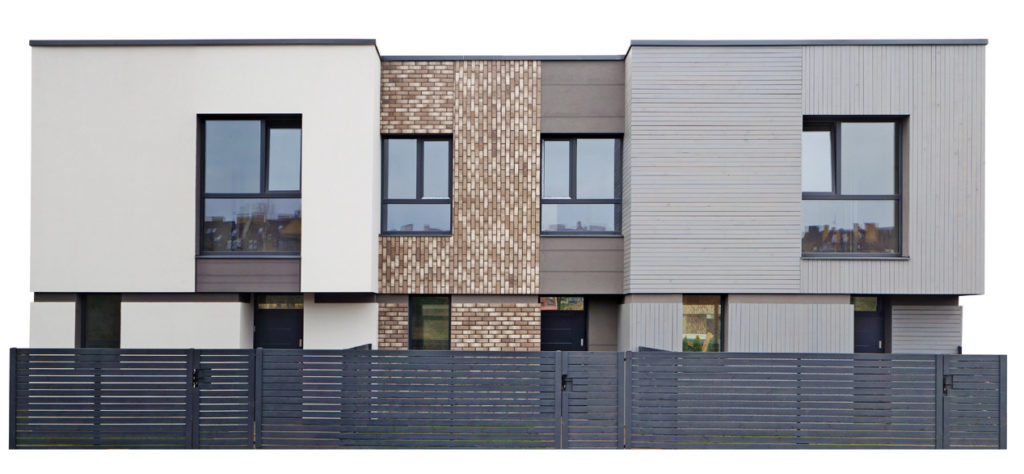
Collaborative approach
The key aspect that has been missing over the many years that we have been trying to perfect the delivery of MMC solutions is undoubtedly the collaborative interaction between the client, the design team and the supply chain. This is down to the fact that our modus operandi is geared towards traditional contracting processes. OSHA and its clients have reviewed this in great detail and its approach to delivery is overcoming
those barriers as a true collaboration.
When you add the additional USPs of OSHA of aggregated demand, from the growing number of social housing providers and local authorities, a well-designed MMC pattern book and zero carbon playbook, all coordinated via an expert MMC project management office and project director, you start to see and feel the real benefits of collaborative engagement from the start of a project, with expert insights at every level,
leaving each expert and authority to shine in their own field of expertise, as a very efficient team.
Finally, the development of a carefully crafted MMC framework (almost two years in the making) along with 13 carefully selected volumetric and panelised system manufacturer partners, across many MMC technologies, ensures that working with OSHA, its processes and partnership
culture, takes away the fears or misconceptions of MMC delivery, now that we are all well on our journey towards high performance, high quality and truly affordable housing.
OSHA’s next step is to build the client base of the alliance from RPs to local authorities, city regions and combined authorities because based on its original mantra, “we are better together than we can be alone”.