The Part L Building Regulations finally kicked in this June, and the message is loud-and-clear: building materials must now deliver sustainable outcomes. Sonia Travis, a Commercial Sales Manager at NorDan UK, shares how an increasing focus on performance and whole-life carbon is shaking up the window and doors’ market, and how NorDan is leading from the front.
It is not that long ago that windows and doors manufacturers responded ultimately to cost, and social landlords and local authorities bought millions of low-cost PVC-U and aluminium products every year (I know, I was selling them)! This made commercial sense at the time, as social developers sought to deliver as many new affordable homes as possible.
This left little financial wriggle room for building material manufacturers, but in recent years this has started to change — and the pace of change is noticeably accelerating. For example, in 2021, Falkirk Council placed an order for NorDan’s high performance timber windows and doors across up to 5,500 homes — the largest single order in the history of retrofitting homes in Scotland.
After extensive market consultation and a competitive tender process, Falkirk elected to fit NorDan’s TopTech reversible windows and balcony doors — both are technical products engineered from sustainably grown timber and clad with an ultra-thin layer of aluminum. Ten years ago, it would have been highly unlikely that a product of this quality would have fitted in these numbers. So, what’s changed? Why do higher-performing building products now constitute viable value?
In short, it’s a combination of three factors: changing building standards, an increasing focus on whole life carbon, and the lengthening of the time in which value is measured.
Rising standards
Let’s start with the Part L regulations, a set of new building standards introduced in England in June 2022, but now fully enforced as of June 2023, following a 12-month grace period.
Part L is in fact an interim set of standards ahead of the implementation of the full Future Homes Standard in 2025. The new standards will reduce carbon emissions from new homes by 30%, and all other new buildings by 27%. The long-term aim is to reduce total building carbon emissions by a minimum of 75% by 2030 to meet wider net zero climate change targets.
The new regulations change the maximum allowable U-values on window and door specification, and the maximum allowable for a window has now been increased by 0.4 Watts-per- meter-square-kelvin (W/m2K), to 1.2W/m2K, and it is anticipated that this figure will drop to 0.8W/m2K in 2025.
The impact of Part L has been noticeable and immediate.
Many of NorDan’s local authority and housing association customers are already specifying to what they anticipate to be the 2025 standard, and recently, two of NorDan’s larger social housing customers have gone back to the drawing-board to re-specify two large affordable housing projects. I’ve also noticed that NorDan has started to win contracts based on the new competitive advantages afforded by Part L.
As a rule, PVC-U, aluminium and composite window frames can only achieve a U-value of 1.2 when triple glazed, whereas the natural insulation qualities of wood mean it can match this performance with double-glazing — and hit U-values as low as 0.74 when triple glazed.
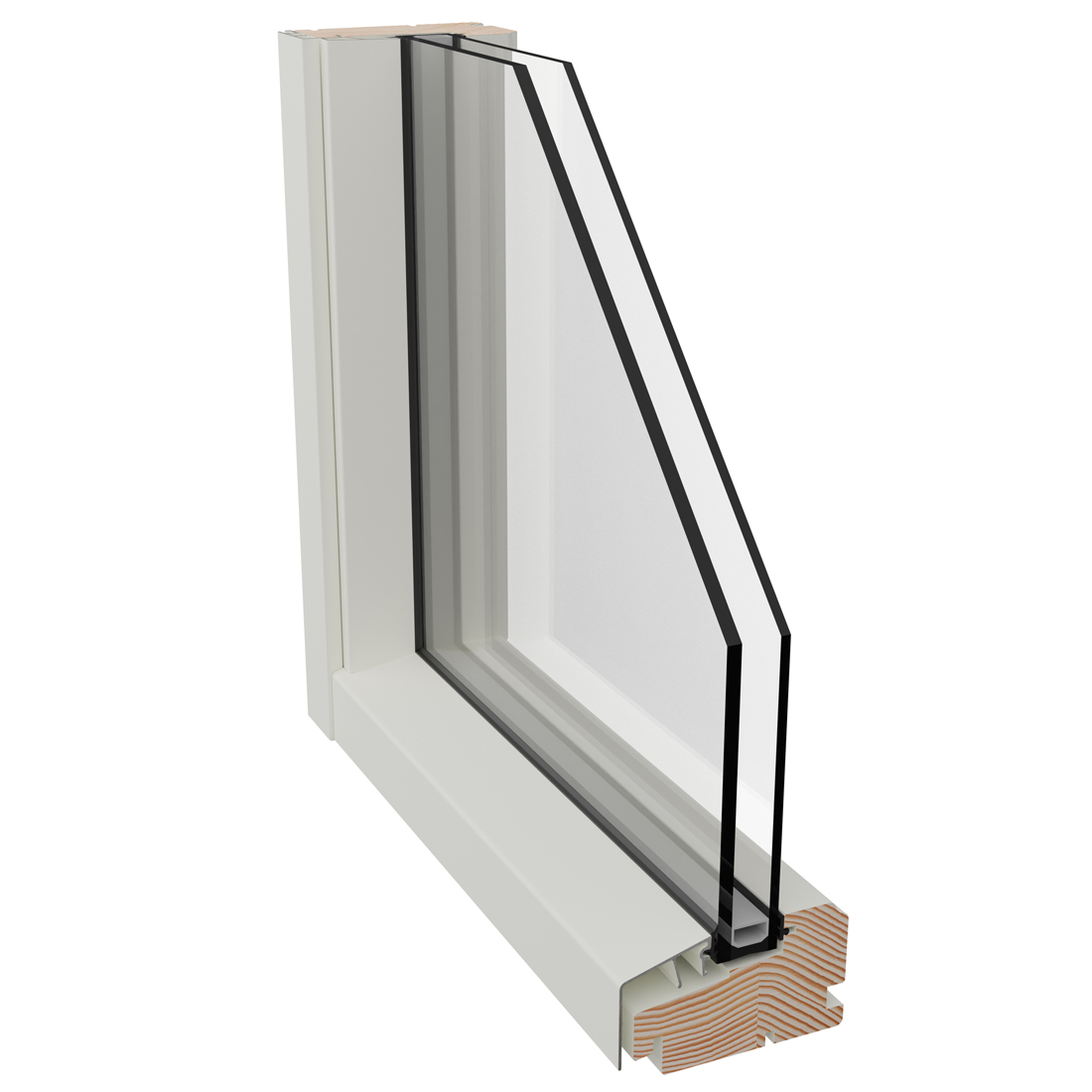
Price and carbon competitive
This has made timber window frames increasingly price competitive, but also carbon competitive, because the extra layer of glazing that non-timber window frames need to achieve the same U-values has an adverse impact on their embodied carbon.
Embodied carbon is the carbon footprint of a material and is increasingly recognised as making up a large percentage of the emissions from construction, and this is gaining more attention from industry and government.
Although Part L only focuses on operational carbon in homes, the industry is pushing for the regulation and measurement of embodied carbon, and legislation is likely in the not-too-distant future. Regardless of legislation, more developers, architects, and specifiers are including embodied carbon in their decision-making but need accurate data to be able to make whole life carbon calculations.
To assist them make informed carbonrelateddecisions, NorDan has invested in Environmental Product Declarations (EPDs) for most of our product range. EPDs are independently verified carbon audits that provide a granular breakdown of all the embodied and operational carbon in a material or product.
Dynamic EPDs
However, the data modelling that generates EPDs can always be improved to reflect the the nuances of customer decision making and combinations of materials used, so NorDan is the first windows and doors manufacturer to launch a more intelligent or Dynamic EPD.
The Dynamic EPDs consider the size and configurations of three-dimensional products and designs, as opposed to two-dimensional product reference, so provide a more accurate calculation.
Continuous investment in digitisation and digital modeling is important as it ensures EPDs deliver an increasingly accurate picture of the environmental impact and performance of materials and keeps pace with other aspects of MMC.
Finally, I’d like to close with a recent quote from Ayo Allu, Director of Design, Technical & Innovation at Clarion Housing Group: “Material costs and the impact of embodied carbon calculations on business performance are increasingly driving the way Clarion Housing Group is constructing its buildings, as is our familiarity with the timber products on the market, and the vast increase in testing data compared to previous years.
“Embodied carbon is already a development consideration within major cities, and the Greater London Authority now has an embodied carbon tool which has to be completed for each new development — with other cities set to follow suit.
“As a development business, we’re now benchmarking our embodied carbon for development and construction activities for the second year running, so we can set reduction targets for ourselves and our supply chain.”
This is crucial, and why the role of high quality and performance timber products is set to continue growing across the UK.
Header image: NorDan has supplied its high performance timber windows and doors to Falkirk Council.