Fiona Coyle from Marshalls Bricks & Masonry explains how Marshalls’ concrete facing bricks met with the performance, sustainability and affordability demands of the aesthetically celebrated North Gate Development, a high quality social housing project in Glasgow.
Concrete bricks are often overlooked in the selection process, with clay bricks usually being favoured, even though they are comparative in many ways. There are also specific benefits of concrete bricks, including their sustainability credentials, which are becoming more important in building project considerations.
A recent project where concrete bricks were extensively used is the North Gate Development in Glasgow. Designed by Architects Page\Park and built by contractor CCG, the North Gate Development in the Gorbals area of Glasgow is among the latest projects for New Gorbals Housing Association. The aim of the project was to transform a constrained brownfield site into high-quality social housing and create a new landmark within the area that also blended with the existing architecture.
A carefully designed series of interconnected towers, the seven-storey North Gate Development, provides a mix of one- and two-bedroomed flats designed to meet the needs of older residents.
The shape of the building means that all 31 flats have dual or triple aspects to maximise natural light and provide views across the city, to create a sense of belonging. With sustainability a core consideration for this development a high-performance building envelope was incorporated, which included a mix of double and triple glazing as well as 72 photovoltaic (PV) panels discretely integrated into the roof. The building’s location and design are also intended to encourage active travel and the use of public transport.
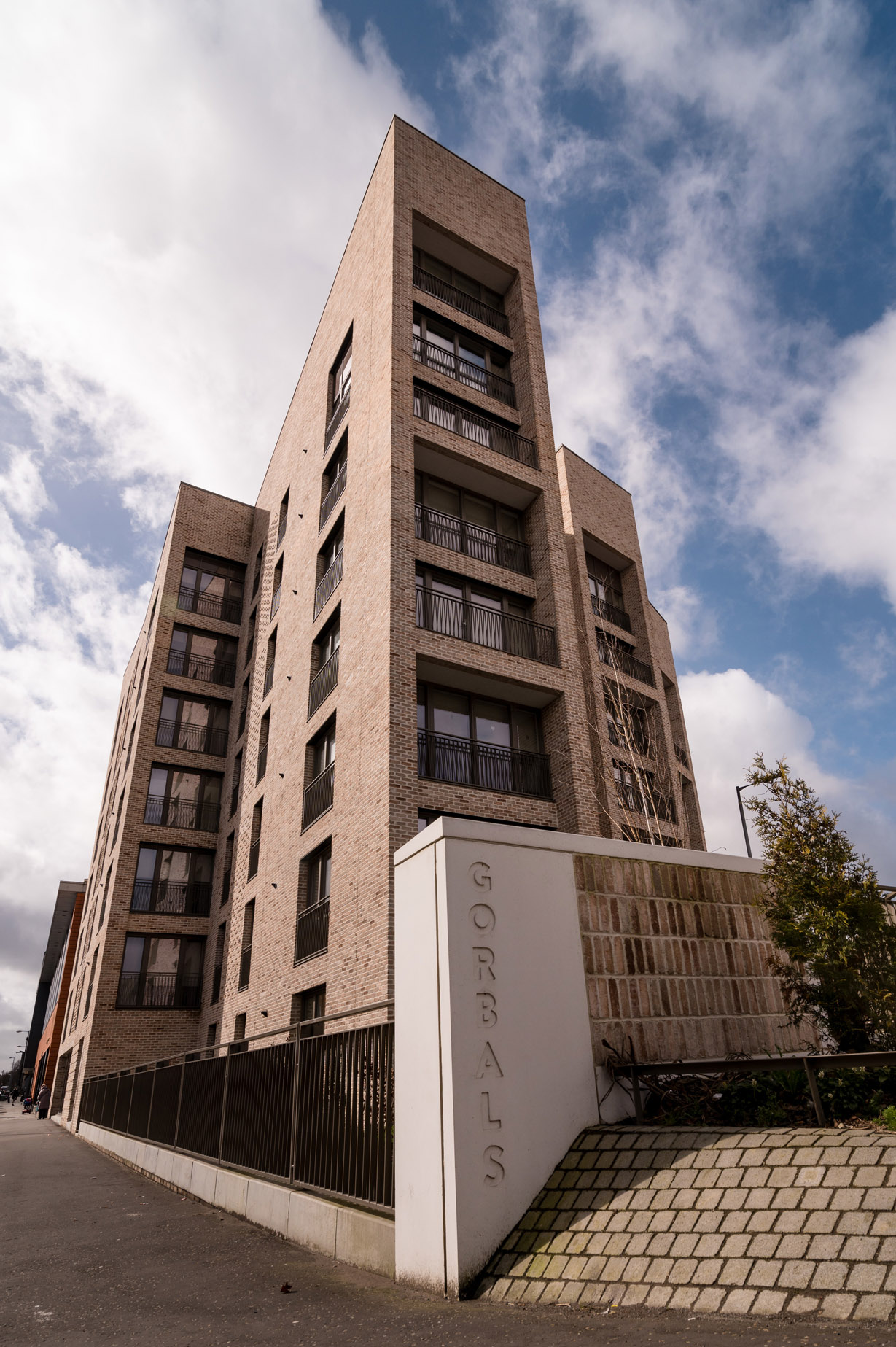
Brick selection process
With brick work featuring prominently, both internally and externally, finding the correct brick for the project was essential. The contractor CCG approached Glasgow Brick Yards (GBY), one of the largest brick stockists and distributers in Scotland, for help finding a suitable product. GBY, CCG, Page\Park and New Gorbals Housing Association were all involved in the selection process. Several Marshalls bricks were identified as possible options.
To help facilitate the final selection, Marshalls and GBY built several test walls at the GBY site nearby. Ultimately, the Marshalls Glencoe Vintage Stock Facing Brick was chosen for its light brown and grey tonal variations, which evokes the traditional blonde sandstone used throughout Glasgow.
The Marshalls facing brick lent itself to this project for several reasons. Firstly, the range of colours available meant that the project team was able to select one that met the requirements of the building and reflected the architectural styles and influences of that area of Glasgow.
Sustainable option
Secondly, for a development where sustainability was at its core, the use of concrete bricks became especially advantageous. Marshalls facing bricks are manufactured using raw materials that are generally sourced from suppliers within a 50-mile radius of the manufacturing site, and use minimal cement in the mix design.
The manufacturing of the concrete bricks also creates minimal C02 emissions. The natural exothermic reaction that takes place is usually sufficient to cure the product. This contrasts with the energy intensive production of clay bricks, which need to be fired in kilns at temperatures between 700 and 1,110°C.
Further to this, concrete facing bricks can sequestrate carbon once in situ, meaning choosing a concrete brick over a clay brick results in a 49.1% carbon saving. Concrete bricks can also be crushed and recycled at the end of their life, diverting construction waste away from landfill.
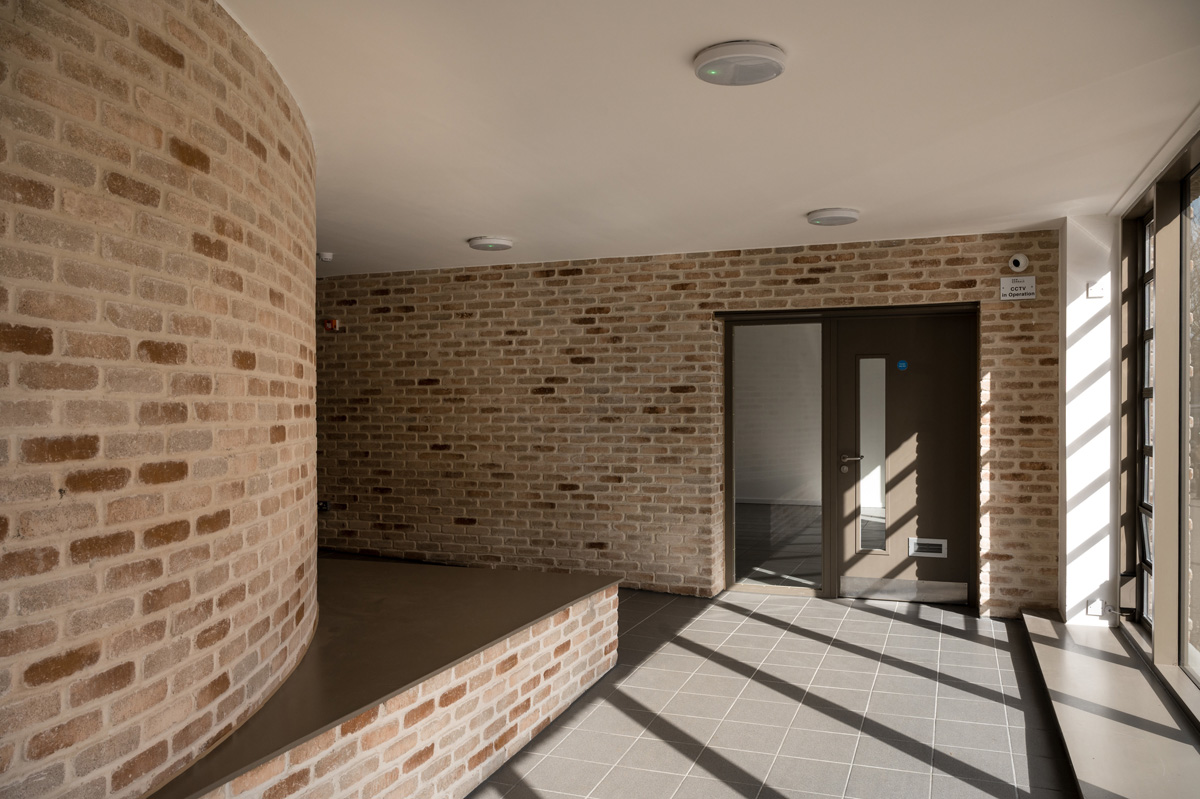
Concrete solution
Cost-effectiveness was another important consideration for the New Gorbals Housing Association on this project. There is often a misconception that concrete bricks cannot be laid as quickly as clay bricks, and therefore leading to higher labour costs. However, this persistent belief is not supported by evidence and is the result of a misunderstanding about the product. For the North Gate Development, the information provided by Marshalls, in addition to CCG’s experience with concrete bricks, reassured the client that the building could be completed on time and to budget.
Despite the numerous similarities to clay and in addition to the lower environmental impact, concrete bricks are still often overlooked. The North Gate Development demonstrates how concrete bricks can be used in a way that supports the aesthetic, environmental and budgetary requirements of a modern social housing development.