In a bid to tackle the effects of climate change, the UK Government has proposed the Future Building Standards and Future Homes Standard, which will see changes to Part L (Conservation of fuel and power) Building Regulations implemented by 2025. Liniar Design & Development Director Chris Armes explores what this means for the social housing sector, offering advice on choosing suitable, cost-effective windows and doors for low carbon, sustainable housing development projects.
From 2025, new residential and non-domestic buildings will need to be much more energy-efficient, producing significantly less CO2 emissions than current standards permit. Within the fenestration industry, U-values are widely used as a measure of window energy efficiency, with a lower U-value meaning better thermal performance.
Incoming regulations are still unknown, but experts are predicting whole-window U-values could be set at of 0.80W/m2K — a drastic change from the current standard of 1.6 for windows in new buildings. Additionally, replacement element requirements (including windows and doors) in existing buildings are also being looked at in terms of energy performance, with the industry waiting in anticipation for an update. Consequently, refurbishment projects will inevitably be required to adhere to more stringent energy efficiency regulations over time.
Whole-window U-values (Uw) add together heat loss through all major components of a window — the frame, glazing, and spacer bars — and it’s important to consider the performance of each element to avoid reliance on costprohibitive add-ons. When a supplier claims a low U-value, it’s advisable to check how this is achieved. For example, is it through a combination of highly efficient components, or is the performance reliant on an expensive, non-standard element such as quadruple glazing or Krypton-filled glazing units?
Considering how a window or door achieves its Uw will help ensure you choose products that deliver the required results in a cost-effective way, making it easier for developers to stay within budget.
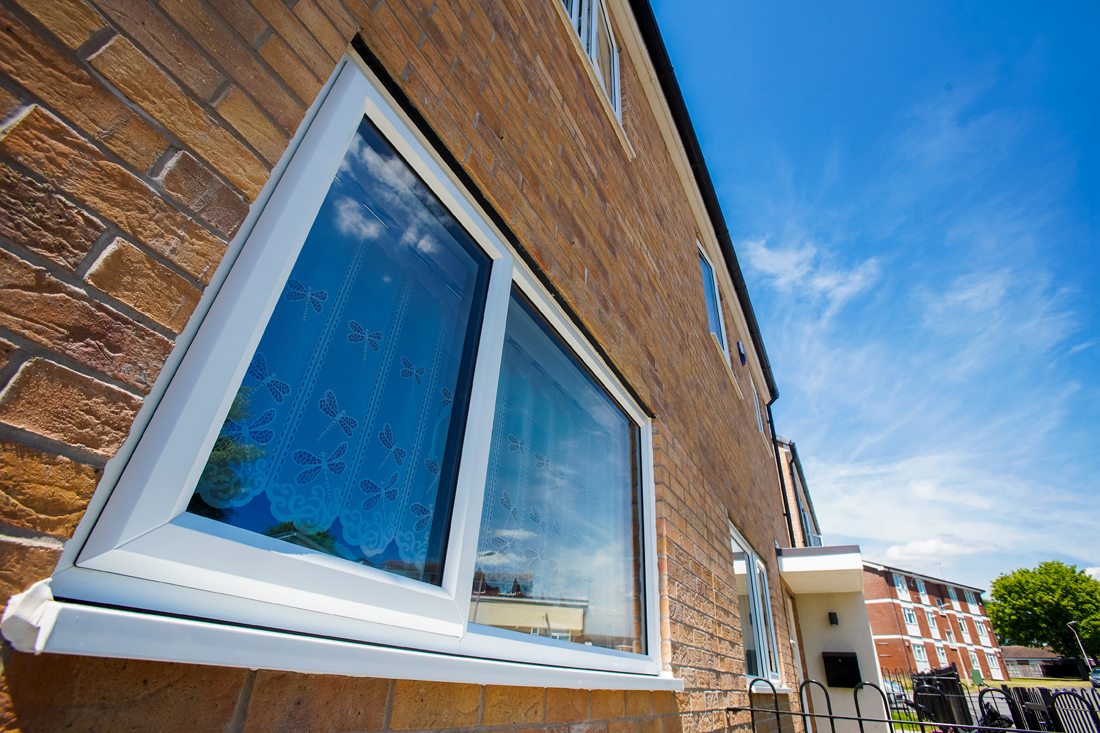
Innovations in window technology
PVC-U has emerged as a highly insulative, thermally efficient material since the 1980s, making it a popular choice for window frames. Whilst the imminent stricter energy efficiency standards will push the limits of PVC-U’s former performance capabilities, British companies have been designing innovative new products, supporting the road to Net Zero, with products already available and being utilised in projects nationwide.
A major benefit of PVC-U frames is the ability to exploit one of nature’s best insulators — air. By using a multi-chambered design, PVC-U window frames trap air inside, creating a thermal barrier that reduces heat transfer and improves energy efficiency. Crucially, the deeper the window and the more chambers inside the frame, or profile, the better the energy performance it can achieve.
Over the years, a depth of 70mm mostly emerged as the industry standard width for domestic PVC-U window profiles. However, the development of 90mm deep multi-chambered window systems such as the Zero|90 range is now capable of a staggering 0.66 U-value with triple glazing, using standard Argon-filled panes of glass. The system offers a clever retrofit solution, Zero|90R, which is ideal for refurbishment projects where
70mm windows are being removed.
This level of energy efficiency not only makes these windows Future Homes Standard-ready, but also takes them into the range of being Passivhaus certified — an energy efficiency specification becoming increasingly mainstream in the face of imminent regulatory changes and a move towards Net Zero societies and low carbon homes.
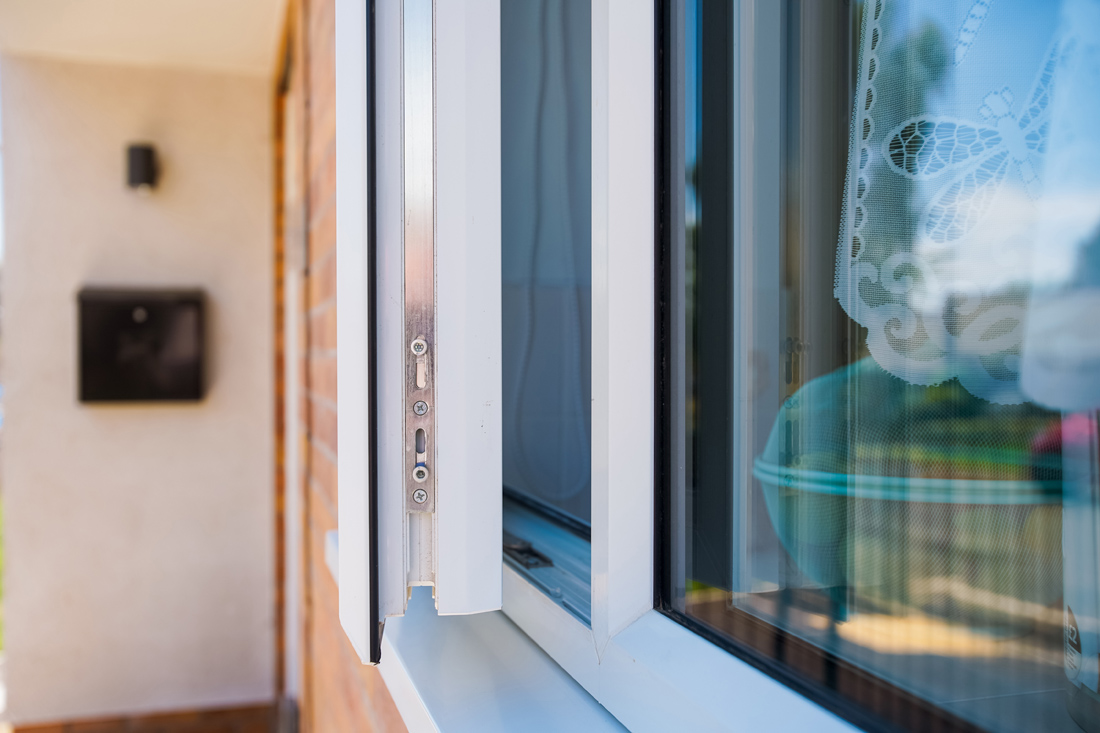
The Passivhaus standard
Passivhaus (a word derived from its German origins — known as Passive House in the UK) is a set of eco-friendly, performancebased design criteria, which ensure compliant buildings, achieve a superior energy performance standard. Rigorous design and construction methods integrate the five principles of robust windows, high quality insulation, airtightness, heat recovery ventilation, and the elimination of thermal bridges (areas in a structure that allow excessive heat transfer in or out).
In 2022, Mansfield District Council commissioned four ultra-low energy homes for social housing rental with the aim of achieving Passivhaus accreditation. As a forward-thinking organisation, Mansfield District Council is proactive in its Green agenda, with a target to halve emissions by 2030 and reach Net Zero by 2050. Passivhaus-certified windows must achieve U-values no greater than 0.80W/m2K.
When Mansfield Council’s Quantity Surveyor (QS) searched the Passive House database for a PVC-U casement window, Liniar’s Zero|90 was the only PVC-U range that appeared. As a British manufacturing company located just a few miles from Mansfield, the range offered additional sustainability benefits and so was specified for the Saundby Avenue project which went on to successfully achieve Passivhaus accreditation — the first of their kind for social housing.
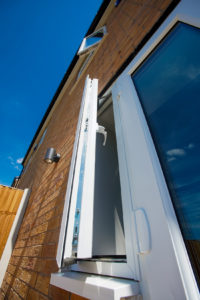
Noise reduction benefits
The resulting measurably energy-efficient homes are not only affordable to run, have significantly lowered carbon footprints, and provide occupants with year-round comfort, they also offer enhanced noise reduction — particularly beneficial in urban areas. A comparable 70mm window reduces external noise by 33 decibels (dB) compared to Zero|90’s 42 dB, helping to ensure occupants get a peaceful night’s sleep. Furthermore, PVC-U is fully recyclable at the end of its useful life and using a system made with recycled components means whole life carbon reductions on top of energy savings.
Preparing for a Net Zero future
As energy-efficient housing takes centre stage and regulations continue to tighten, local authority and housing association decision-makers must have access to innovative products that can help to future-proof the developments under their management.
British-designed PVC-U window systems capable of meeting more stringent energy-efficient standards are beginning to enter the market. Nevertheless, manufacturers must be clear about how products are achieving their energy performance so that specifiers can make well-informed decisions and choose the most cost-effective solutions for their projects.
Header image: Liniar’s Zero|90 range was specified for Mansfield District Council’s Saundby Avenue project.