Mark Kimberley, Head of Fast Trak at Gripple, explains the importance of knowing the embodied carbon of products used in all construction projects.
As the pressure mounts to deliver more sustainable construction projects, products and components that support this objective are in high demand. Carbon reduction, and the embodiment of that, is just one element of consideration and with buildings responsible for 39% of all the carbon emissions in the World (according to the World Green Building Council), there is little wonder that there is such a focus on this in the built environment.
To facilitate this, and to enable local authorities and contractors to make more informed choices, an increasing number of product manufacturers are working hard to provide as much information as possible regarding the sustainability of their products, to assist specifiers satisfy CO2 reduction requirements.
What is embodied carbon?
As manufacturers begin to focus on the carbon embodiment of their products and how they integrate into the overall embodied carbon of a building, it appears that there are considerable improvements to be made. The term embodied carbon refers to the emissions created during the construction of a building and the carbon footprint of the materials used within it, taking into consideration the manufacturing process, installation, and transportation of the products for example. So how are manufacturers addressing the problem especially for key components in commercial construction?
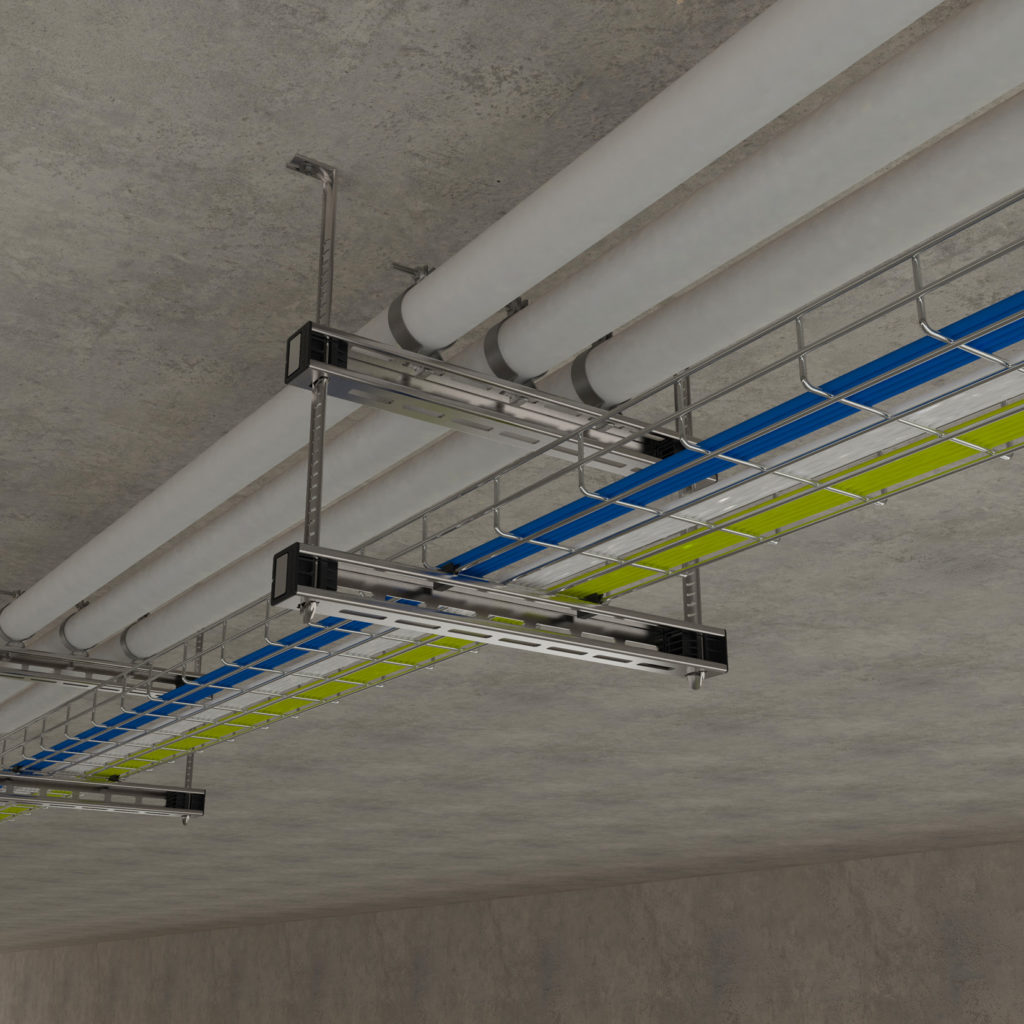
Embodied carbon and containment systems
M&E suspension systems are a key component for safely grouping cables, ductwork and pipes, and are utilised in most commercial projects. Finding a way of doing this that supports sustainable building practices, Modern Methods of Construction (MMC) and carbon embodiment is now a primary consideration for architects, specifiers, facilities managers, and installers.
A prefabricated solution such as Fast Trak by Gripple is a system that makes M&E installations easy. There is no need for hot work permits, cost and time efficiencies are improved, and site health and safety is simplified. Most importantly, the embodied carbon of projects is reduced due to the specific way in which the product is manufactured and installed.
Components are made to exact specifications, reducing waste, whilst the installation can be carried out with just one engineer, and has been proven to be six times quicker to install when compared with traditional threaded rod systems.
Tangible results
In a project carried out for a new-build education establishment in Milton Keynes, the Fast Trak team produced detailed project design drawings along with labour, material weight and embodied carbon savings as part of the proposed solution.
Speaking on the distribution relationship with Gripple, the Cambridge Manager for Edmundson Electrical says: “It has been great to work alongside Gripple to push such an innovative product. Not only does it reduce the install time for the contractor, but the reduction in the carbon footprint is also a big win. In a time where environmental impact is at the forefront of our decision-making process, it is great to have manufacturers within our network who are leading the way.”
Indeed, the total embodied carbon saving for the project is around a third less when compared with the traditional threaded rod system (Fast Track 4,706kg versus Traditional Method 7,666kg).
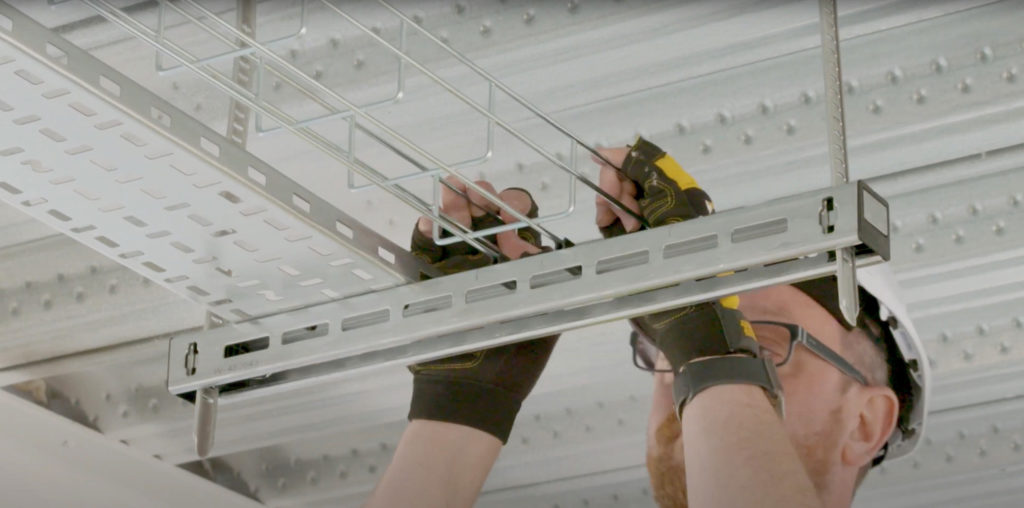
Supporting modern construction
As embodied carbon becomes ever present in the specification and installation of projects, manufacturers of products will have to demonstrate figures and those commissioning projects will be obliged to choose those providers that bring the most favourable environmental benefits.
In the race to net zero, all elements of our economy will have to find ways of making carbon related savings and the construction sector is paving the way in terms of its expectations from manufacturing, installers, and transport professionals who work on construction projects.
In addition, embodied carbon reductions support the BREEAM certification process reinforcing its importance. BREEAM ‘recognises and reflects the value in higher performing assets across the built environment lifecycle’. A product that minimises waste, increases safety, reduces cost and is all together more efficient, ticks all the boxes when it comes to integrating into sustainable and responsible construction projects, both in the UK and across the globe.
Header image shows a contractor fitting Gripple’s Fast Trak Suspension System.