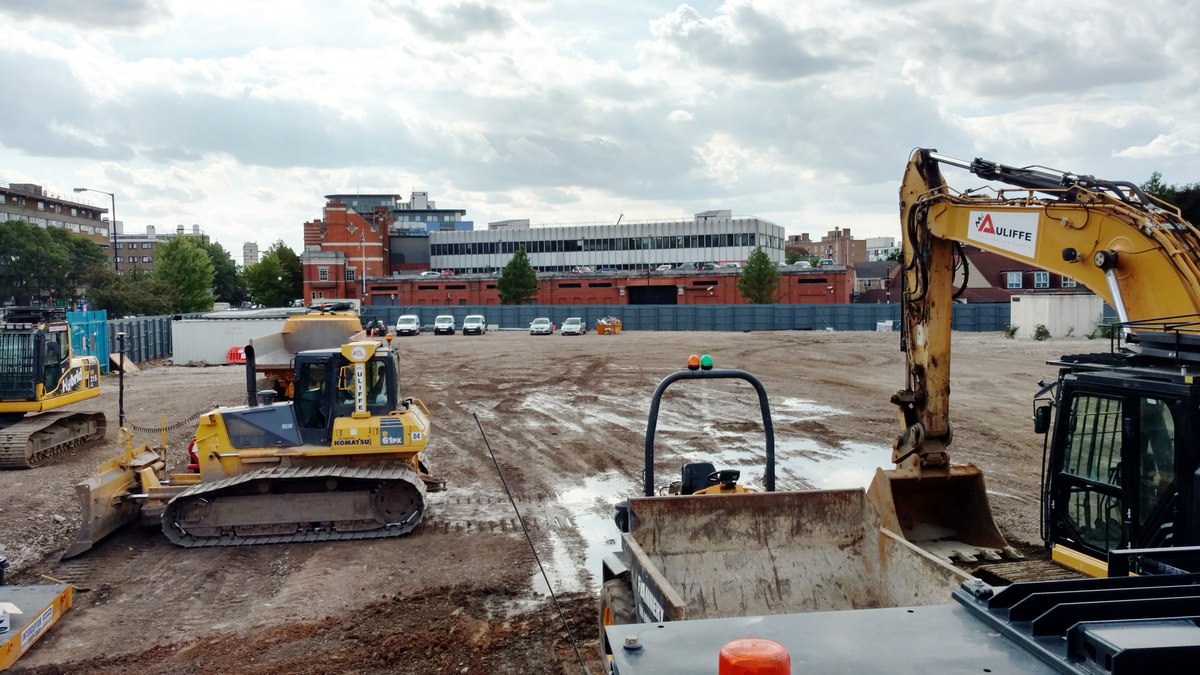
John McAuliffe, Managing Director of the McAuliffe Group, offers advice on overcoming the barriers to brownfield development.
The barriers to developing on brownfield land often centre on planning and the abnormal costs and issues associated with the historical use of the site. Given the housing shortage, these barriers can cause significant headaches for local authorities and housing associations that need to actively build new homes. For example, if the brownfield land being developed involves a change of use — often the case when pursuing new-build housing schemes — it will require a complex and costly planning application, including time and costs for pre-application discussions.
Brownfield sites have often been long established and subsequently are now located in heavily built up areas. This requires consideration on the surrounding infrastructure and public facilities, which are often at capacity and already underinvested. Brownfield sites also tend to have limited frontage and access points and, consequently, are landlocked by a multitude of either residential or commercial land, which may come with different potential objections due to the impact on the areas in close proximity.
There is still a substantial amount of public miseducation regarding contaminated land. There is a job to be done by contractors to inform the public that there are significant health, safety and environmental protocols that must to be followed when remediating contaminated land.
Complexity and cost
Another reason brownfield land is more difficult to get planning on is because it costs more to clean up. This means contributions to councils and any allocation of social housing can be limited, causing issues with planners. But that’s not to say that many councils do not actively promote the use of both public and private sector brownfield land for housing and commercial development. The key is to make the process easier for all parties involved to bring more housing to fruition on land that is ripe for development — as cost-effectively and quickly as possible.
Here are just some of the works that may need to be carried out on Brownfield land:
- Demolition of existing buildings — often including asbestos removal.
- The removal and processing of subsurface concrete and deep obstructions.
- Remediation of soil and groundwater contamination, especially when previous use involved chemicals and fuel.
- Managing the related earthworks and geotechnical improvement of the soil.
- Tackling Japanese Knotweed and other invasive weeds.
- Removing former shallow mine workings.
Typically the cost of remediating brownfield sites ranges from £25,000 to £100,000 per acre, excluding piling and grouting costs. More complex sites, such as former landfill sites, require more extensive remediation, which can range from £300,000 to £500,000 per acre. It’s vital for specialist contractors like McAuliffe to work closely with government agencies and councils and housing associations to carry out a full cost and time analysis of the necessary factors prior to development. This will help to break down some of the barriers to building on brownfield and accelerate its pathway through planning and delivery.

New homes for Peckham
In May 2017, McAuliffe was contracted to remediate the derelict site of the former Wood Dene council estate in Peckham, London, to accommodate 333 new homes for Higgins Construction and Notting Hill Housing Association (NHHA). The site required a £825,000 full-scale remediation and ground engineering exercise on 10,000mᶟ of contaminated materials to ensure construction works could be safely completed.
Demolished in 2005, the 1.47-hectare derelict site inherited a layer of crushed demolition material from a previous demolition contract, comprising Asbestos Containing Materials (ACMs) and asbestos fibres at hazardous levels. McAuliffe developed an Environment Agency approved materials management plan (MMP) and Environmental Permit to remediate material for re-use onsite, avoiding unnecessary landfill deposits and traffic disruption.
Remediation works were split into three phases. The first involved initial regulatory approval, licensed asbestos removal, demolition, MMP approval, Environmental Permit with Deployment Plan and additional site investigation. The second stage focused on remediation and the validation of the top 1m of asbestos-contaminated demolition material under the Environmental Permit. Lastly, McAuliffe carried out the excavation of underlying soils down to 4m to remove all obstructions, providing an engineered development platform.
Sustainable remediation techniques included the asbestos remediation, obstruction removal and earthworks solution into a concurrent workflow enabling a 40% programme reduction, delivering the project in under 12 weeks. This ensured Higgins could get onsite well ahead of projections and begin building.
Remediation strategy grids were uploaded to in-house 3D GPS enabled excavators, allowing real-time onsite location and tracking, generating as-built information on demand. Reassurance sampling and remediation of 10,000mᶟ of material was carried out, enabling re-use in the piling mat. What’s more, material containing ACM was picked, stockpiled and analysed — allowing the remediation of 4,800mᶟ of suitable material for construction.
McAuliffe excavated and re-compacted underlying soils; concrete obstructions were processed for re-use, ensuring 8,600mᶟ was recycled onsite for the piling mat, and 3,500mᶟ of non-hazardous and hazardous soils were diverted from landfill — all in line with approved guidelines.
By working closely with Higgins and NHHA at every stage of the process, the client saved £3m through re-use of materials onsite, which also saw the removal of 2,000 lorry loads from the roads and diverted 10,000mᶟ of material away from landfill.