How a more collaborative approach to tender design could benefit public sector specifiers by Jon Sheaf, Major Projects Manager, AluK.
Adopting a more collaborative approach to design for aluminium windows, doors and curtain walling can save public sector specifiers months on procurement and reduce costs. It has already been proven to work in the new build private sector and is something which could potentially be extended into the public sector as well.
It involves a level of trust of course between client, consultant, supplier and contractors, but the effect that it has in de-risking the tender process for the client means it is worth exploring on complex and large-scale projects.
It works by putting the client at the centre of the process and allowing the preferred systems house to work with them and the design team on the technical and commercial elements of the project at pre-tender stage. Inviting input from an aluminium systems house into a RIBA 4 system design means that the commercial and design iteration of the fenestration elements can take place pre-bid and not be left for the façade contractors to interpret, whilst they are trying to build a quotation.
The results of that are: time saved on the normal procurement route, tender returns that are more accurate and comparable, a system backed by a systems house, and greater cost certainty for the client. There is also a bigger incentive for busy façade contractors to submit bids because the information is accurate and complete, with the need for far fewer RFIs.
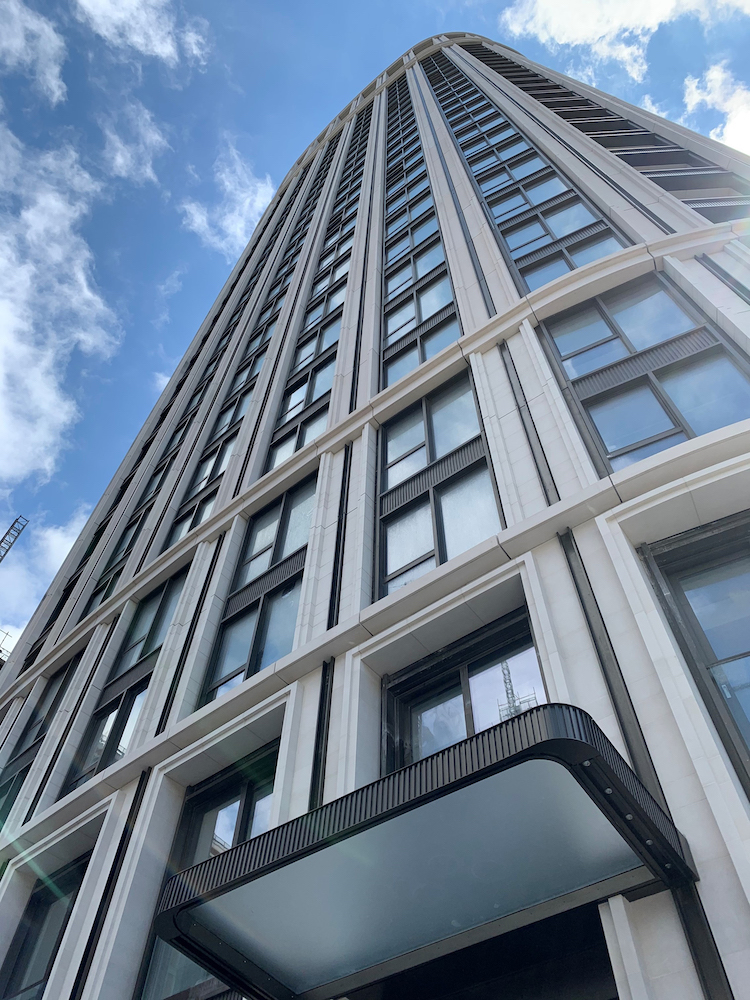
Probably the best example we’ve seen of the approach in action was at the 110m, 29-storey curved on plan Westmark Tower, recently completed by Berkeley Homes at the West End Gate development in Marylebone. The Tower features more than 14,000m2 of unitised curtain wall, nearly 250 lift and slide doors, 750 concealed vents and 60 swing doors.
Almost at the outset, AluK was able to work with the client and the architect to create a unitised façade solution for the post-tensioned concrete frame which satisfied the design intent, whilst designing in sensible savings on metal and accessory costs. For example, the challenge of how to dead load the unitised curtain walling cells back to a post tensioned concrete frame was overcome by designing a 3-dimensional floor bracket. Once the RIBA 4 design was produced and the optimum solutions were clearly communicated in the tender documents, only three RFIs were issued by the tendering façade contractors!
The completed façade installation features more than 2200 unitised cells of three principal configurations. Each floor comprises: a vision cell, typically housing a concealed vent and full height glass units, a panel cell, specifically designed to carry articulated GRC (Glass Reinforced Concrete) feature piers and spandrels, and a recessed balcony cell with an integrated floating glass balustrade. Cost savings came from minimising the number of bespoke profiles and gaskets and focusing on a value engineered solution from the beginning.
From a specifier’s perspective, this approach requires early engagement, a commitment to regular workshops, sharing expectations with the design, fabrication and installation teams, and a collaborative ethos. The benefits in terms of reduced timescales and cost certainty more than justify that commitment, however.
Header image: Westmark Tower in Marylebone features AluK curtain walling.