Ben Edmondson, Technical Director at façades specialist Aliva UK, comments on external wall insulation’s pivotal role in the UK retrofit agenda.
External wall insulation systems are at the forefront of Modern Methods of Construction and given more than a third of the heat in a building is lost through its walls, high quality EWI, also known as ETICS (External Thermal Insulation Composite Systems), are a must for any energy-conscious building projects or retrofit schemes.
The demand to accelerate the UK’s transition to Net Zero comes as a cost-of-living crisis deepens, with the energy efficiency of homes being a huge conversation. Retrofitting properties to reduce energy bills has become a huge talking point recently, particularly for the most deprived areas of society, as energy prices soar.
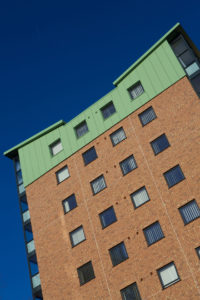
EWI systems are a key measure in improving existing housing stock to achieve more efficient thermal values and reduce both heat loss and energy costs. Using insulants such as Expanded Polystyrene or Mineral Wool, EWI can make a remarkable contribution to retrofit initiatives and to the Net Zero Carbon agenda.
Improving thermal values and reducing energy bills can be combined with a wide range of aesthetic finishes, which ensure regenerated housing stock and estates can achieve an improved quality of life for the householders.
Fabric first — retrofit relevancy
EWI is a pivotal cladding material to consider in the retrofit landscape for social housing stock owned by local authorities and housing associations. External wall insulation measures help to reduce carbon and greenhouse gases across local authority areas spanning the UK. When combined, the impact and combined U-value data from across these local authority areas is helping to positively contribute to the UK’s overarching Net Zero Carbon goals.
It is for this prime reason that EWI is regarded as one of the most effective ways to thermally upgrade existing buildings and why it is ideal for local authorities and housing associations with ageing social housing stock, often dating back to the 1940s, 50s and 60s.
Qualifying as a fabric first solution, this seeds the cladding solution’s grant funding relevancy under the Social Housing Decarbonisation Fund (SHDF), Great British Insulation Scheme (GBIS) and the fourth phase of the Energy Company Obligation ECO4.
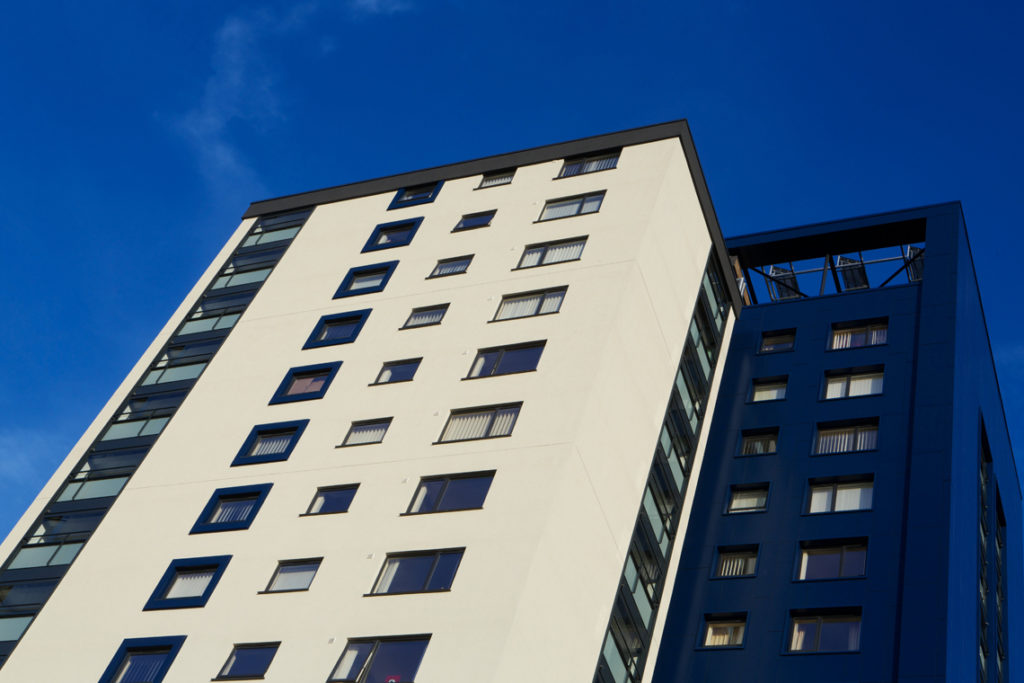
Fabric first — results fast
Alongside qualifying as a fabric first solution, and the inherent benefits this brings to
retrofitting in itself, EWI systems deliver immediate results — when compared to energy efficiency measures like solar photovoltaic panels or ground source heat pumps, which take time to aggregate/yield their results, benefits and savings.
EWI instead brings immediate advantages — improved thermal values are experienced straight from installation, which is swiftly followed by reductions in residents’ energy bills due to lower energy consumption required. EWI also generates improved U-values, which equals energy saving for the planet. It’s more relevant than ever as a retrofit solution for stock owning local authorities and housing associations to enhance their homes, to the benefit of residents, as it helps save money on fuel costs in the current cost-of-living crisis.
Certification and standards
Quality, standards, longevity and reliability of EWI systems are pivotal for the public sector’s procurement landscape and reassurance on the safety of products. Aliva UK’s Termok8 EWI systems, for example, are fully tested and certified for retrofit applications under BBA Certificate 11/4841.
This BBA certification is relevant for masonry, concrete, blockwork and no-fines concrete substrates, which is ideal for the many solid wall houses, masonry and concrete properties and high-rise properties owned by local authorities and Registered Providers.
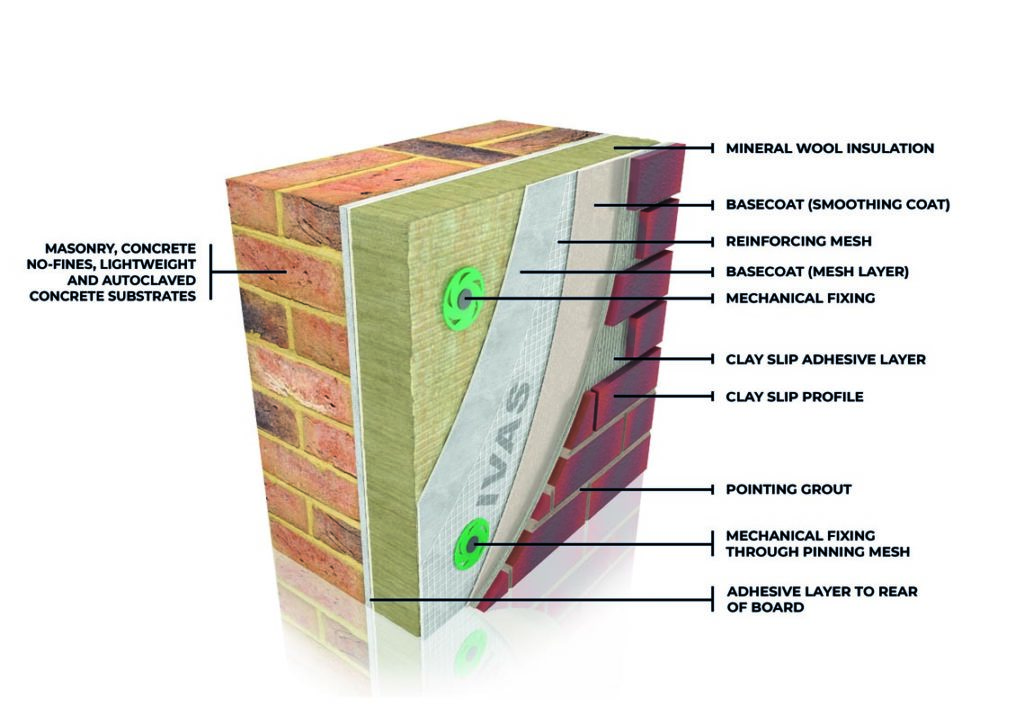
Aliva’s EWI Termok8 ranges hold fire performances to Euro Class EN 13501-1 of A1, A2,s1,d0 and B and its coloured textures have also been awarded the Fraunhofer Institut fur Bauphysik certification for algae and fungal resistant coatings. As an EWI specialist and system designer, Aliva is also a member of the recognised External Wall Insulation trade body. The Insulated Render and Cladding Association (INCA) has a 40-year history and a membership structure that represents contractors, system designers and associates. INCA membership is a marker of reputable EWI specialists with recognised standards of competence.
Although neutral colours are most common, Aliva has a range of over 400 colours spanning its Termok8 standard palette and its STRONG and REFLECT range, these include vibrant colours from pillar box red, to darker shades with solar reflective properties. Aliva can also offer fully certified clay and lightweight slip finishes, which can be used in isolation or combined with the textured finishes to create a traditional looking building façade.
Versatility of insulants
EWI is incredibly versatile, insulants come in a range of thicknesses to deliver energy-efficient results for a specific project’s thermal requirements or can be used to create a particular design intent.
Optimising a nationwide retrofit programme
The UK has some of the oldest housing stock in Europe, it’s estimated that some 37.8% of the UK’s houses were built before 1945. As INCA highlights as part of its 2024 call to government, to optimise the delivery of an effective nationwide retrofit programme to improve these 10+million homes, there needs to be a prioritisation of the fabric first approach. EWI delivers the greatest cost saving impact on fuel bills of all energy efficiency measures as well as delivering significant health benefits to tenants and residents.
For more information on Aliva UK’s EWI range visit https://alivauk.com/what-we-do/ewi-and-brick-slips/
Header image: EWI solution installed on the Ennismore Avenue low-rise housing scheme