A. Proctor Group provides a fabric first approach to improving performance and efficiency in social housing.
The treatment and design of retrofits are critical in the drive to meet the net zero targets and the requirement to improve the performance and efficiency of social housing. A popular measure of improving energy efficiency in existing housing is installing insulation following a fabric first approach to building design. In a retrofit, a fabric first approach must maximise airtightness and insulation.
Fabric first design is a core principle of Passivhaus construction. The principles of Passivhaus, in climates like the UK, include very high levels of insulation; extremely high performance windows and doors (including thermally broken and insulated frames); very low levels of air permeability; thermal bridge free construction; and a mechanical ventilation and heat recovery system. The Passivhaus standard requires buildings to use less than 15KWh/m² to maintain their habitable temperature.
The Passivhaus Trust also published the EnerPHit standard, a slightly more lenient standard for retrofit. An EnerPHit building can use up to 25kWh/m² each year in space heating or cooling demand and have an air permeability of up to one air change per hour at fifty pascals, compared to the 0.6 required for Passivhaus. These values are derived from the volume of the building, unlike building regulations, which stipulate an air exchange through the surface of the building. In England, this regulated value is 8m³/m²h@50Pa, while in Scotland it is 7.
Both English and Scottish regulations also provide details of a notional dwelling, which achieves 5m³/m²h@50Pa. It is not just in airtightness that Passivhaus and EnerPHit require more stringent targets than the Building Regulations. U-values are also generally tighter, as one of the core design principles is reduced heat loss through the building fabric. The external envelope of any Passivhaus building should have a U-value between 0.1 and 0.15.
Climate zones
Building Regulations vary by country, while the EnerPHit standard specifies a U-value with respect to the climate. The UK has three climate zones for this purpose: a warm temperate climate, found in Devon, Cornwall, and London; a cool temperate climate, which most of the UK comes under; and a cold climate, found in Northern Scotland and other highland areas.
The U-value targets also allow for differences based on where the insulation is installed. The required U-values for warm temperate climates are 0.3W/m²K if external insulation is used, and 0.5 if the insulation is internal. Most of the UK falls into the cool temperate climate zone, where the targets for an EnerPHit construction are 0.15 with external insulation and 0.35 with internal, and the coldest regions of the country have targets of 0.12 and 0.3W/m²K, respectively.
Building Regulations in England and Wales state that refurbishing external walls in residential buildings should bring their U-value down to 0.3W/m²K, or 0.55 if insulation can only be applied inside the cavity. It also allows existing walls with U-values below the threshold of 0.7W/m²K to remain unimproved. Scotland requires all external walls to achieve 0.17W/m²K, though allows for localised areas in excess of this where unavoidable.
Roofs require more stringent requirements in both EnerPHit and Building Regulations. Part L was updated in June, so all retrofitted roofs in England and Wales require a U-value of 0.16W/m²K unless the existing roof is already below the threshold of 0.35. In Scotland, all roofs are required to achieve 0.12W/m²K.
The Passivhaus and EnerPHit standards don’t differentiate between roofs and walls, instead providing a single value for the whole external envelope. However, the standard doesn’t make the same allowances for internal insulation in roofs as for walls, as the insulation would not restrict the floor area. This means that, for most of the country, a roof renovated to EnerPHit standards would need to achieve 0.15W/m²K. Hence, a warm pitched roof with rigid insulation between and under the rafters would likely mean having 150mm
between and 30mm below, assuming standard PIR insulation.
The UK’s housing stock is among the oldest in Europe, with over 20% of homes being more than 100-years old. The Energy Efficiency Standard for Social Housing sets an additional target for government-owned social housing. All social housing must achieve an EPC rating of B by 2032, creating an enormous requirement to retrofit these buildings with energy-efficient solutions.
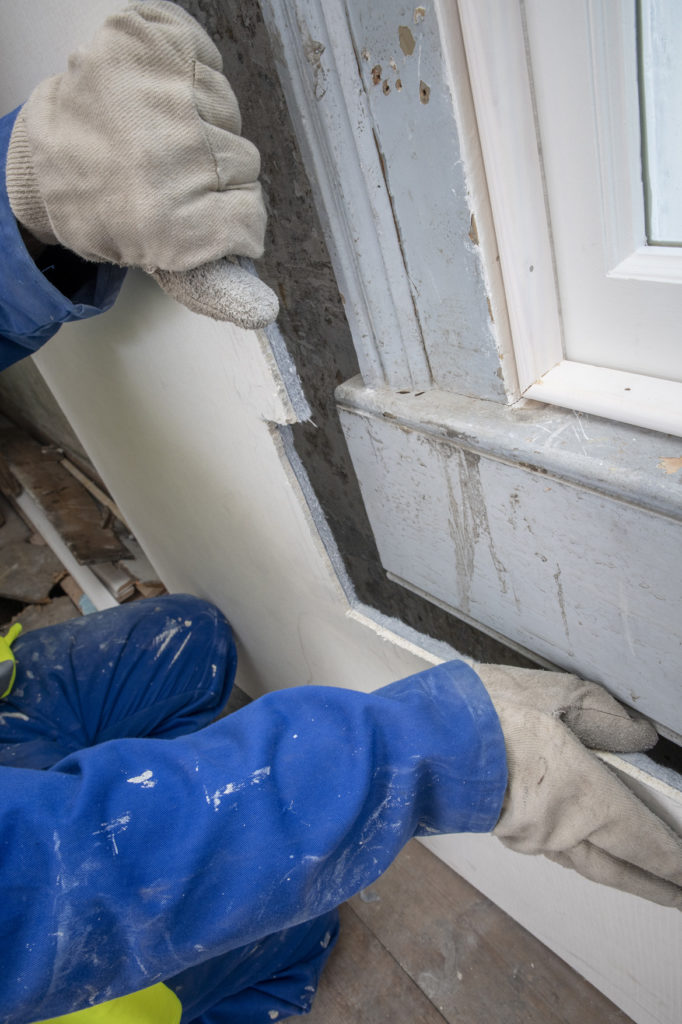
External or internal solutions
Cavity wall construction means that some buildings can insulate within the cavity. Whilst an effective way to use an otherwise empty void, it must be installed carefully to ensure it is evenly applied and the insulation does not create a bridge across which moisture can track.
The cavity is often insufficient to bring buildings to their required U-values, particularly if the renovation is aligned with the EnerPHit standard. A typical cavity wall using brick and block might have a U-value of 1.7W/m²K without accounting for internal finishes. Insulation in the cavity might reduce this to around 0.6 with EPS insulation, which would not meet Scotland’s U-value requirements or the EnerPHit standard but almost achieve regulations in England and Wales, with their slightly lower requirements. If the internal lining brought it down to 0.55, it would be acceptable to building control.
Framed wall constructions are easier to insulate as they include a large cavity within the wall. If the internal linings can be replaced, filling these studs, or updating the insulation within them, is an excellent way to improve thermal efficiency. A vapour control layer can also be added inside the frame, reducing the risk of condensation, and providing airtightness. Many roofs are of similar constructions to framed walls and can usually be insulated between their rafters and have a VCL applied to manage the risk of condensation.
When these options are unachievable, the only way to insulate an existing wall would be to provide insulation internally. This solution has challenges. First, it takes up floor space. Many smaller rooms cannot accommodate the depth of insulation required to bring a wall down to the necessary U-value requirements of
0.3W/m²K.
A standard 215mm brick wall would take over 100mm of mineral wool insulation to meet this target, which could be up to 140mm when bridging is accommodated. Considering this would typically be offset from the wall with a cavity, such a system could require over 200mm of space from each external wall.
Building fabric efficiency
Based on years of extensive research and industry expertise, the A. Proctor Group has developed a range of solutions to improve the energy efficiency of the fabric of the building.
A specific solution for airtightness in retrofit construction is Procheck Adapt, a vapour variable vapour control layer certified as a Passive House component for airtightness. This variable permeability intelligent vapour control layer adapts its vapour resistance to suit the environment, becoming vapour tight in the winter and vapour open in the summer. So, the membrane adapts to changes in humidity levels and allows the structure to dry out in the summer and sunny days in spring and autumn while protecting it from moisture overload in the winter and cold, wet days.
The Spacetherm range comprises high-performance aerogel insulation that can be bonded to various boards to suit specific applications. Spacetherm Blanket is a versatile material that is both vapour permeable and hydrophobic. It can be bonded to a magnesium oxide board to produce Spacetherm Multi. This can be as thin as 16mm, including 10mm of insulation and a 6mm board, making it ideal for breaking the cold bridges typically found at window reveals. It allows walls to be insulated to a thinner depth than otherwise possible. For example, 45 – 50mm of insulation would bring a typical wall down to the 0.3W/m²K required for Building Regulations and EnerPHit. In addition, Spacetherm cold bridge strips can easily be applied to minimise cold bridges.
Addressing the challenge of internal insulation, Spacetherm Wall Liner is a thin thermal laminate of about the thickness of a standard layer of plasterboard. It consists of 10mm of Spacetherm insulation and a 3mm Magnesium Oxide board adhered to the wall to provide significant thermal retention compared to the uninsulated wall.
In meeting our critical net zero targets and the need to improve the energy efficiency of social housing, a fabric first approach is crucial in retrofit construction.
Header image: Procheck Adapt is a vapour variable vapour control layer certified as a Passive House component for airtightness
For more information on Procheck Adapt visit https://proctorgroup.com/products/procheck-adapt
For more information on Spacetherm visit https://proctorgroup.com/products/spacetherm